


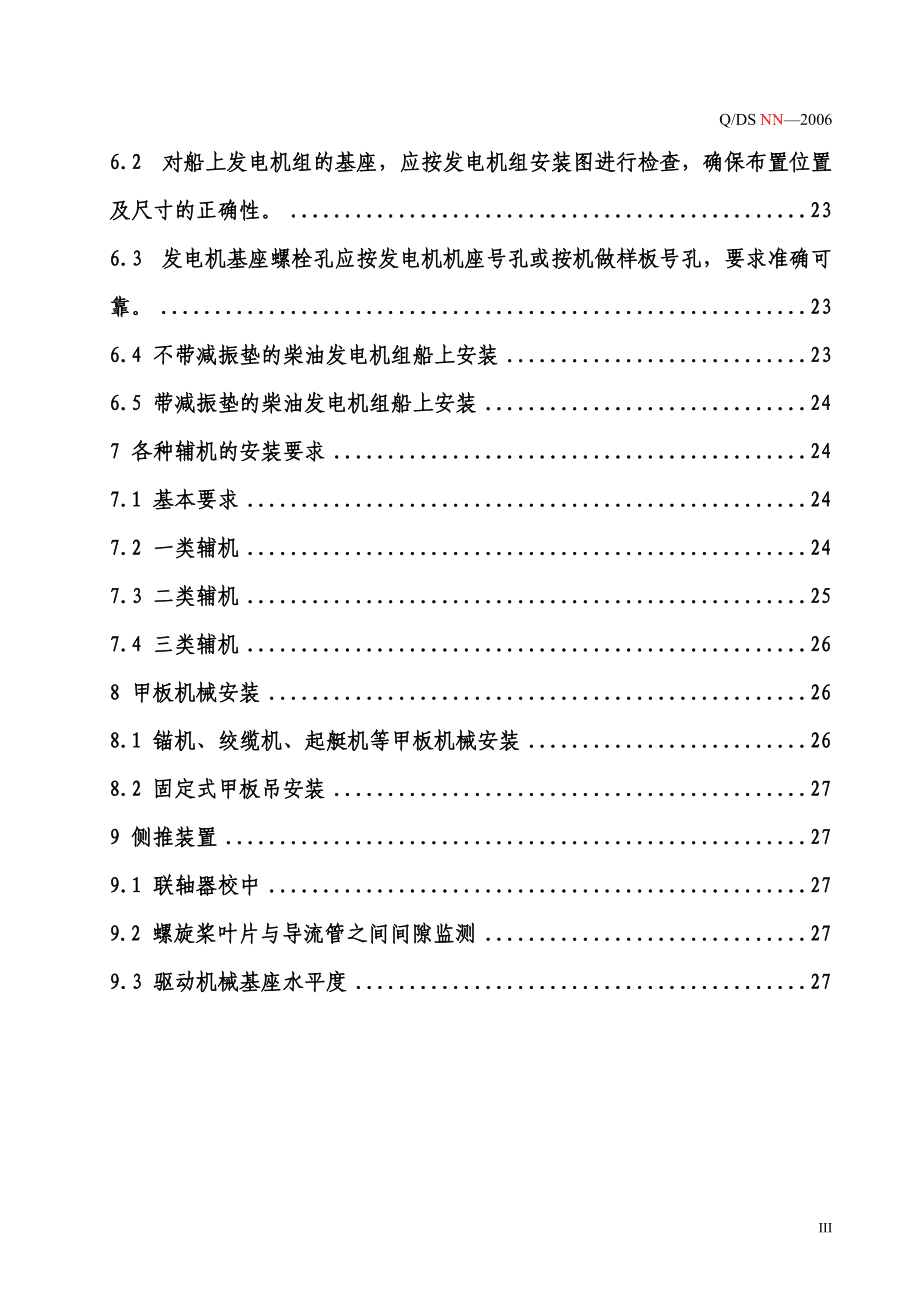

版權說明:本文檔由用戶提供并上傳,收益歸屬內容提供方,若內容存在侵權,請進行舉報或認領
文檔簡介
1、Q/DL 482004大連船舶重工集團有限公司 發布2006年8月1日實施2006年8月1日發布船舶建造質量標準(輪機部分)Q/DS NN-2006 代替Q/DL48-2004Q/DNS.J04.006-2005 Q/DS大連船舶重工集團有限公司企業標準1Q/DS NN2006目 次前 言III1 范圍12 軸系中心線確定及軸系安裝12.1 照光或拉線確定軸系中心線12.2 艉軸管加工32.3 艉軸管鏜孔后中心復查軸系復光32.4 主機基座螺栓孔確定及加工42.5 艉軸管軸承的加工和安裝42.6 中間軸與艉軸法蘭連接螺栓孔及螺栓52.7 無鍵聯接螺旋槳與艉軸裝配62.8 有鍵聯接螺旋槳與艉軸裝
2、配72.9 中間軸承安裝82.10 艉軸船上安裝82.11 螺旋槳船上安裝92.12 中間軸吊裝103 主機船臺/塢內吊裝113.1 主機在船上裝配對周圍環境的要求113.2 主機吊裝前對基座的要求113.3 主機吊裝的方法113.4 主機安裝結束后的清潔及保護123.5 主機安裝結束后的設備保養124 軸系排軸找正124.1 排軸條件124.2 排軸要求124.3 對于B&W低速柴油機船上定位124.4 對于非B&W低速柴油機船上定位174.5 主機往復運動件檢查174.6 主機側向拉緊裝置175 舵裝置安裝185.1 舵桿、舵銷、舵葉車間內加工185.2 舵銷套及舵桿套加工
3、及安裝185.3 舵桿、舵銷與舵葉研配185.4 舵桿與舵機或舵柄連接錐面研配205.5 拉舵系中心線205.6 舵系軸承孔加工215.7 舵鈕襯套加工要求及安裝225.8 舵系各部件船上安裝226 主柴油發電機組安裝236.1 上船前應在車間對柴油機曲軸臂距差檢查一次,并做好記錄。236.2 對船上發電機組的基座,應按發電機組安裝圖進行檢查,確保布置位置及尺寸的正確性。236.3 發電機基座螺栓孔應按發電機機座號孔或按機做樣板號孔,要求準確可靠。236.4 不帶減振墊的柴油發電機組船上安裝236.5 帶減振墊的柴油發電機組船上安裝247 各種輔機的安裝要求247.1 基本要求247.2 一類
4、輔機247.3 二類輔機257.4 三類輔機268 甲板機械安裝268.1 錨機、絞纜機、起艇機等甲板機械安裝268.2 固定式甲板吊安裝279 側推裝置279.1 聯軸器校中279.2 螺旋槳葉片與導流管之間間隙監測279.3 驅動機械基座水平度27IV前 言為了統一大連船舶重工集團有限公司內部不同工場的船舶輪機安裝質量要求,在對原標準Q/DL48-2002和Q/DNS.J04-2005對照比較并求大同存小異的基礎上進行完善、補充和統一。本標準在編制過程中,參照了中國船舶行業標準(CB/T4000-2005)等相關標準。 本標準由大連船舶重工集團有限公司標準化委員會提出。 本標準由大連船舶重
5、工集團有限公司船舶及海洋工程設計研究所標準室歸口。本標準起草單位和修訂單位:船舶及海洋工程設計研究所工藝一、二室、機裝二室。本標準起草人:楊玉波、王運才、于嘉琦。本標準審定人:宮國璽船舶建造質量標準輪機部分1 范圍本標準規定了船舶主機、軸系、舵系、輔機、甲板機械、側推裝置等設備的安裝和驗收要求。本標準適用于各類民用船舶的建造,其它船舶產品可參照執行。2 軸系中心線確定及軸系安裝2.1 照光或拉線確定軸系中心線利用給定的船體艏艉基準點,采用軸系照光或拉線的方法來確定軸系中心線。2.1.1 軸系照光或拉線的條件2.1.1.1 要求在不受陽光曝曬及溫度急劇變化的情況下進行,一般在晚間或陰天,以避免船
6、體變形影響軸系中心線的準確性。2.1.1.2 要求機艙前隔壁以后,上至舵機平臺以下的船體分段裝配、焊接、火工矯正等船體工事基本結束,主甲板分段就位。2.1.1.3 發電機組及其它主要設備進艙結束或用同等重量的物體壓載。2.1.1.4 機艙前隔壁以后的船體墊墩、支柱要合理牢固,不許任意移動。2.1.1.5 軸系艏、艉基點的設置必須牢固可靠?;c的支座應使用寬度為320mm的槽鋼,側向及縱向用適當的角鋼拉緊。要求焊接牢固、穩定可靠并確認無誤。同時舵系的上下基點也應確認無誤。2.1.1.6 停止振動及有嚴重噪音干擾的工作。2.1.2 用照光或拉線的方法確定軸系中心2.1.2.1 照光確定軸系中心線:
7、將照光儀(準直望遠鏡)置于船的艏(艉)基點位置上,使照光儀的光束重合于艏艉兩基準點的中心。在艉軸管的前、后端各設一個光靶,調整光靶中心,使其與光束重合。2.1.2.2 拉線確定軸系中心線:通過艏、艉基準點拉鋼絲線,如圖1。 圖1 軸系拉鋼絲線確定中心線示意圖鋼絲線撓度計算公式:y=qx(L-x)(1)2T(1)式中:y 在計算點上的撓度,單位:mm;q 每米鋼絲線的重量,單位:g/m;x 從計算的一點到端點之間的距離,單位:m;L 拉線兩端點之間距離(拉線與軸中心線兩交點),單位:m;T 鋼絲線的掛重,單位:kg。具體參見表1規定。表1 鋼絲線有關參數鋼線直徑mm斷面積mm2鋼線質量g/m推薦
8、掛重kg掛重極限kg0.300.07070.5671012.70.400.12560.99152022.60.500.19631.54203033.40.600.28272.22304048.02.1.3 照光或拉線需檢查的項目2.1.3.1 舵系中心線與軸系中心線偏差值軸系中心線與舵系中心線的允許偏差按式(2)計算:(2)式中:允差,單位為毫米(mm);L船只總長,單位為米(m)。2.1.3.2 主機基座面板上平面距軸系中心線高度,允許偏差為±10mm。2.1.3.3 主機基座面板內邊每側距軸系中心線距離,允許偏差為±5mm。2.1.3.4 中間軸承或齒輪箱等基座面板頂面
9、距軸系中心線高度,允許偏差為±10mm。2.1.3.5 中間軸承或齒輪箱等基座面板寬度中心與軸系中心線的偏差,允差為±10mm。2.1.3.6 鏜孔前,軸系中心線與艉管中心線偏差應滿足鏜孔機加工的要求。2.1.4 確定艉軸管加工基準拉線或照光的所有檢查項目都合格后,確定艉軸管加工基準。2.1.4.1 照光確定軸系中心線后,確定艉軸管前、后端鏜孔的加工基準,按光靶中心用規圓線的方法在艉軸管前、后端面上劃出艉軸管加工基準圓線及檢查線并打沖點作標記(劃線前應將端面的上下左右位置約50 mm×50 mm的面積打磨光滑),同時確定艉軸管前后端面的加工量,并在艉軸管前后端面劃
10、加工線和檢查線。2.1.4.2 拉線確定軸系中心線后,安裝艉軸管前、后端基準塊,根據鋼絲線的下垂量計算,確定艉軸管前、后端的鏜孔基準,同時確定艉軸管前、后端的加工量且劃加工線和檢查線。2.2 艉軸管加工2.2.1 選鏜桿某一點為測量點,以基準點或基準圓線為基準找正,調整鏜桿,檢查鏜桿安裝的正確性,鏜桿的中心與基準點或基準圓線允許偏差為±0.03mm。(圖2)圖2 艉軸管加工示意圖2.2.2 艉軸管內孔按圖紙要求加工。2.2.3 艉軸管內孔加工精度符合表2要求。表2 艉軸管內孔加工精度 mm鏜孔后內孔直徑200400400600600800800圓度/圓柱度0.030.040.050.
11、062.2.4 加工后的艉管內孔及各端面表面粗糙度要求不高于Ra 3.22.3 艉軸管鏜孔后中心復查軸系復光2.3.1 將準直望遠鏡放置在艉軸管艉端,光靶放置在艉軸管艏端,按艉軸管內孔中心找正,允許偏差為±0.01mm。2.3.2 通過準直望遠鏡中心和艉軸管前端光靶中心,檢查艏基點中心,水平方向允許偏差見表3,垂直方向偏差按表3的數值允許適當放寬,但最大不可超過數值的2倍。表3 艏基點中心水平方向允許偏差艏艉基準點間距 m151525253535允許偏差 mm±2±3±3.5±52.3.3 檢查舵系中心線與軸系中心線偏差,要求同2.1.3.1。
12、2.3.4 測量艉軸管成品后端面到舵線的距離,按圖紙要求尺寸允許偏差±5mm。2.3.5 也可采用拉鋼線的或激光方法測量艉軸管的同心度。2.4 主機基座螺栓孔確定及加工2.4.1 按主機基座最后一排螺栓孔中心至艉軸管成品后端面距離,確定主機基座螺栓孔中心沿艏艉方向的位置,并在主機基座上劃出與軸線垂直的主機基座最后一排孔的中心線,如果在船臺上造船應考慮船臺的斜度,見圖3。圖3 船臺上建造時主機基座螺栓孔位置的確定2.4.2 用常規方法,根據主機安裝圖尺寸劃出主機基座上所有螺栓孔的中心線,并號孔。2.4.3 用鉆機鉆削或用專用氣割機切割基座螺栓孔,切割后孔內壁應打磨光順。2.4.4 主機
13、基座采用間隙配合形式的螺栓孔加工要求2.4.4.1 螺栓孔圓度、圓柱度應不大于1mm。2.4.4.2 螺栓孔縱向相鄰孔中心距偏差不大于0.5mm,累計偏差不大于2mm。螺栓孔中心相對于軸系中心線應對稱分布,其位置度偏差不大于1mm。2.4.5 主機基座采用過盈配合形式的螺栓孔加工要求2.4.5.1 螺栓孔的位置度要求同第2.4.4.2條。2.4.5.2 螺栓孔鉸孔后,其圓度不大于0.015mm,圓柱度不大于0.02mm。2.4.5.3 螺栓過盈量為0mm0.02mm。2.5 艉軸管軸承的加工和安裝2.5.1 艉軸管前、后巴氏合金軸承加工2.5.1.1 艉軸管與艉軸承之間的安裝通常為盈配合,其過
14、盈量應滿足設計要求。艉軸管安裝之前,應對二者的相關尺寸進行精確測量,以確認其準確無誤。如果軸承廠家有具體要求,應按廠家的要求進行,同時要考慮軸承中心抬高問題(按圖紙要求)。2.5.1.2 艉軸(螺旋槳安裝后)在艉軸管軸承內的相應傾斜角度必須符合軸系校中計算書中的有關要求,如果不符合,艉軸承應進行補償量加工。2.5.1.3 軸承的外徑加工精度按表2要求進行。2.5.1.4 巴氏合金軸承外圓與艉軸管內孔平均過盈量一般為0.01mm0.04mm,具體按圖紙要求配制加工。2.5.2 艉軸管前、后巴氏合金軸承壓裝2.5.2.1 巴氏合金軸承壓裝負荷應符合軸承制造廠推薦要求。當制造廠沒有推薦要求時,按照表
15、4進行。表4 巴氏合金軸承壓入負荷型 式艉軸管軸承內徑 mm壓入負荷 kN艉軸管前軸承艉軸管后軸承艉軸管巴氏合金軸承(油潤滑式)30050070300150600500900150600350100090015080035012002.5.2.2 艉軸管軸承壓裝后,其內徑應進行檢測并符合圖紙要求。2.5.3 艉軸管非金屬軸承艉軸管非金屬軸承,按照制造廠的具體要求進行加工和安裝。2.5.4 艉軸管及其軸承組件以環氧樹脂澆注定位艉軸管及其軸承組件以環氧樹脂澆注定位時,參見第4.3.8條和專船工藝要求。2.6 中間軸與艉軸法蘭連接螺栓孔及螺栓2.6.1 中間軸與艉軸在車間對中(此項工作也可在船上進行
16、)2.6.1.1 中間軸與艉軸在車間進行對中,支承距離應符合圖4要求。圖4 中間軸與艉軸對中示意圖圖中:a1=b1=0.2L1 a2=b2=0.2L22.6.1.2 兩法蘭找正對中,平面接觸應緊密,0.03mm塞尺不能塞入,曲折、偏移不大于0.02mm。2.6.1.3 按孔配制螺栓,并打印配對記號。2.6.1.4 鉸制孔表面粗糙度要求應不高于 Ra1.6,最低不低于Ra3.2。2.6.1.5 鉸制孔的加工精度要求。孔徑50 mm時,其圓度和圓柱度應0.01 mm;其圓度和圓柱度應0.02mm。2.6.1.6 法蘭螺栓按孔配制,對于普通鉸制螺栓,應加工成0.005mm0.030mm的平均過盈量或
17、按設 計要求,采用液態氮進行冷縮裝配;對于液壓拉伸螺栓(含間隙配合螺栓),應根據制造廠家提供的說明書進行加工與拆裝。2.6.1.7 螺栓孔加工后,兩端面應锪平并與螺栓孔中心線垂直,螺栓裝配后,螺栓頭用0.05 mm塞尺不能塞入。2.6.1.8 螺栓外圓的表面粗糙度為 Ra1.6。2.6.1.9 螺栓外圓的加工精度要求。孔徑50 mm時,其圓度和圓柱度應0.01 mm;孔徑50 mm時,其圓度和圓柱度應0.02 mm。2.6.1.10 兩法蘭對中交驗后,用臨時螺栓緊固。2.6.2 按圖紙要求配制加工中間軸和艉軸法蘭連接螺栓孔和螺栓。2.7 無鍵聯接螺旋槳與艉軸裝配2.7.1 螺旋槳與艉軸樣板加工
18、2.7.1.1 采用“公/母”結構形式的樣板加工螺旋槳轂錐孔和艉軸錐體。2.7.1.2 制作樣板的材料用A級鋼,厚度一般為6mm8mm。2.7.1.3 樣板制作要求:樣板應平直,結構堅固、輕便,不得有變形,其直線度、對稱度和垂直度均0.03,公/母樣板應成對提交檢驗,縫接觸應緊密,0.03mm厚度塞尺檢查,插入距離不大于30mm長度,正反兩面應配合一致。2.7.1.4 公樣板成品后應該有明顯錐度起始線和螺旋槳錐孔加工用檢查線標記,見圖5。圖5 公樣板示意圖公樣板上錐度起始線與螺旋槳錐孔加工用檢查線之間距離“S”的確定,見下式。S=L1+L2+L3 mm (3)(3)式中:L1 螺旋槳錐孔預留軸
19、向研配量,見表5;L2 無鍵聯接螺旋槳油壓安裝計算書給出的壓入量,單位:mm;L3 螺旋槳安裝到位后,槳轂錐面大端端面至艉軸錐度起始線的距離,由設計圖紙中給出。 表5 螺旋槳錐孔軸向研配量 mm螺旋槳錐孔大端直徑 100>100200>200300>300400>400500>500600>600700軸向研配量354658697108109122.7.1.5 螺旋槳錐孔大端加工尺寸按孔用樣板上標記的檢查線進行加工,上下允差1 mm,其錐度符合樣板的要求,用0.05 mm塞尺檢查不能塞入或局部塞入長度20mm2.7.1.6 螺旋槳軸錐部的加工按軸用樣板進行檢
20、查,其錐度應符合樣板的要求,用0.05 mm塞尺檢查不能塞入或局部塞入長度20 mm2.7.1.7 樣板在每次使用之前,應進行仔細的檢查校對以確認樣板的準確性。2.7.2 艉軸錐體與螺旋槳錐孔的研配2.7.2.1 以艉軸錐體研配螺旋槳錐孔,每25mm×25mm區域內接觸斑點不少于3點,接觸斑點應均勻分布,接觸面積應不小于75%,錐孔兩端的著色要比中部更為均勻,不得有間斷,用0.03 mm塞尺檢查兩端局部插入深度10mm,寬度15mm。2.7.2.2 艉軸與螺旋槳大端面的垂直度,用直角尺現場檢查不大于0.15mm/m。2.7.2.3 根據無鍵螺旋槳液壓安裝計算書要求確定其實際壓入量2.
21、7.2.4 螺旋槳液壓安裝起始點應根據常規的作圖法或無鍵螺旋槳液壓安裝計算書的要求確定2.7.2.5 測距百分表的觸頭應垂直于槳轂前端面。每壓入1 mm記錄一次其對應的軸向和徑向油壓,壓裝過程應確保平穩、安全2.7.2.6 壓裝到位后,首先泄掉槳轂內的油壓,保持液壓螺母的油壓15min左右,使槳轂能可靠地固緊在螺旋槳軸錐體上。然后泄掉液壓螺母的油壓。最后檢查測距百分表有無變化,并予以確認2.7.2.7 預裝結束后,應進行螺旋槳液壓拆落。此時,將液壓螺母松開并向后退出適當的距離,槳轂與液壓螺母之間應墊有大約30 mm厚的木板,剩余間隙應略大于螺旋槳的液壓安裝距離。2.7.2.8 慢慢升高槳轂內的
22、油壓直到螺旋槳從螺旋槳軸上退下為止。記錄退下螺旋槳的最大油壓。 2.8 有鍵聯接螺旋槳與艉軸裝配2.8.1 有鍵連接螺旋槳與艉軸的加工、研磨與裝配要求與無鍵聯接螺旋槳相同。2.8.2 艉軸鍵槽2.8.2.1 鍵槽工作面粗糙度為Ra3.2,鍵底及兩側邊應平直。2.8.2.2 艉軸鍵槽的前端應做成雪撬形或匙形,并應光滑、圓順,鍵槽根部應按照圖紙要求加工圓角。2.8.2.3 固定鍵的螺栓孔深度不得超過螺栓直徑尺寸(不包括鍵)。2.8.3 鍵與艉軸鍵槽、螺旋槳鍵槽研配2.8.3.1 鍵嵌入艉軸鍵槽內,0.04mm厚度塞尺不允許塞入縫隙。2.8.3.2 鍵槽底平面與鍵涂色檢查,接觸面積應在40%以上,聽
23、聲音不允許懸空。2.8.3.3 鍵與螺旋槳鍵槽接觸應虛沾,塞尺檢查應小于表6所列數值。 表6 鍵與鍵槽允許間隙 mm鍵 寬3050508080100100130塞尺厚度0.040.050.060.072.8.3.4 鍵的頂部應有2%鍵高的間隙,但不得超過1mm。2.9 中間軸承安裝2.9.1 銅套材料牌號應符合設計要求。2.9.2 中間軸承的定位安裝工作應在軸系校中的最后階段進行。2.9.3 用塞尺測量軸承間隙,軸承前后兩端的左右間隙應為裝配間隙的40%60%,上部間隙等于裝配間隙,下部用0.05 mm塞尺不允許塞入銅套內徑尺寸應符合圖紙要求,推薦平均過盈量見表7。2.9.4 底座墊片應著色檢
24、查,每25 mm×25 mm面積內不少于兩個色點,接觸區域70%,允許局部有縫隙,但0.05 mm塞尺插入深度10 mm,寬度15 mm。2.9.5 底座螺栓如鉸孔,則其圓度和圓柱度3050的孔0.01 mm,50以上的孔0.015 mm;螺栓與孔的配合應過盈量為00.02 mm。2.9.6 螺栓孔加工后,兩端面應锪平并與螺栓孔中心線垂直,螺栓裝配后,螺栓頭用0.05 mm塞尺不能塞入。2.10 艉軸船上安裝2.10.1 艉軸管艏、艉密封裝置2.10.1.1 艉軸管艏、艉密封裝置在車間進行液壓試驗,試驗介質采用實用滑油,壓力0.2MPa,保持5min,密封裝置不得有滲漏。2.10.1
25、.2 艉軸管密封裝置在船上安裝后,進行壓油試驗。利用艉軸管滑油重力油箱高度,將系統注滿油至重力油箱規定油位,使艉軸管承受重力油壓,檢查重力油箱油位,在6小時內不應有變化。2.10.2 艉軸承溫度傳感器在安裝前、后應分別檢查導電性和絕緣電阻。2.10.3 艉軸管后密封裝置潤滑油管按照圖紙要求安裝并進行密性試驗。2.10.4 艉軸管徹底清潔交驗。2.10.5 艉軸上船安裝,測量并記錄艉軸管前后軸承間隙,測量位置應符合圖6要求。2.10.6 密封裝置船上安裝就位后,應根據專船工藝文件進行密性試驗。圖6 艉軸與艉軸管軸承間隙測量位置示意圖2.11 螺旋槳船上安裝2.11.1 安裝前應準備的主要工具:液
26、壓螺母的專用扳手,點式溫度計,百分表及磁性表座,高壓液壓泵組兩套及高壓軟管等,參見圖8。2.11.2 螺旋槳裝到艉軸上推靠后,主機1號缸活塞在上死點時,選一個槳葉垂直朝上(有特殊要求者除外)并與艉軸法蘭或聯軸節記號在同一個位置。圖7 螺旋槳安裝示意圖2.11.3 根據已被認可的無鍵螺旋槳油壓安裝計算書中0和35壓入量數據,以及現場實測的螺旋槳溫度,用插入法確定現場安裝時實際壓入量數值,并在現場取得船東、船檢認可。壓入時艉軸錐體與螺旋槳槳轂溫度應相同。2.11.4 按無鍵螺旋槳液壓安裝計算書中給出的起始壓力值,用液壓螺母給螺旋槳施加軸向起始壓力,此時螺旋槳在螺旋槳軸上的相對位置,即為實際壓入量的
27、起始點。2.11.5 當螺旋槳液壓安裝計算書中沒有規定軸向起始壓力時,可按船廠常規值300kN500kN進行干壓法確定。2.11.5.1 首先,當認為螺旋槳已被推靠之后,軸向液壓泵升壓至起始點壓力P(此時徑向液壓泵不泵壓,稱為干壓),停止泵壓后,將測距表調到零位,然后再繼續干壓1點2點,連接P、P1或P2連線,并將其反向延長相交于橫座標A點,則該點與零位點之間距X0即為初始壓入距離。(見圖9)2.11.5.2 以A點為基準來測量壓入量。此后,軸向和徑向液壓泵同時泵壓(稱為濕壓),在螺旋槳壓入過程中,每壓入1mm記錄一次軸向和徑向油壓,壓入到位后,根據記錄值繪制螺旋槳壓入曲線圖(見圖8)。圖8
28、螺旋槳壓裝曲線示意圖2.11.6 螺旋槳壓裝結束后,記錄百分表讀數,首先逐漸卸掉徑向油壓,停留20分鐘之后,觀察百分表有無變化,最后再卸掉軸向油壓。2.11.7 上述工作交船東、驗船師認可后,液壓螺母靠一人之力扳緊,然后再打緊5°10°。2.11.8 從螺旋槳小端端面經液壓螺母外圓至艉軸后端螺母做連續記號,作為檢驗螺母松動的標記,并將0、35壓入量之數據和起始壓力值,分別打印在槳轂上。2.12 中間軸吊裝2.12.1 在吊主機前中間軸進艙。2.12.2 根據軸系校中計算書安裝中間軸的兩個臨時支撐。2.12.3 將中間軸著落在兩個臨時支撐上。3 主機船臺/塢內吊裝3.1 主機
29、在船上裝配對周圍環境的要求3.1.1 避開下雨天氣。3.1.2 機艙周邊應無電焊、氣刨火花飛濺和打磨、拋丸等產生粉塵性的作業。3.2 主機吊裝前對基座的要求3.2.1 主機基座應平整,平面度不大于5mm,長度和寬度允差4mm。.3.2.2 當采用僅有鋼質調整墊片時,基座保證少許內高外低,一般傾斜度約為1:100,至少平齊;一旦內低外高時,允許進行機加工修正,加工后的基座厚度應滿足船級社的最低厚度要求。3.3 主機吊裝的方法a)在船臺吊裝主機,由于起重能力的限制,對于大型主機需分體吊裝;對中型主機可分層吊裝對小型主機可整體吊裝。b)在塢內對大中型主機可分層吊裝,對小型主機可整體吊裝。3.3.1
30、主機分體吊裝的步驟(B&W公司低速柴油主機)3.3.1.1 主機在上船之前對主機的零部件要在車間或在船臺下進行清潔(重點注意的問題)。3.3.1.2 主機機座安裝找正機座在自由狀態下檢查和調整水平度,水平度要求:縱向0.05mm/m,縱向全長0.2mm,橫向全長0.1mm。3.3.1.3 曲軸吊裝a)曲軸清潔后吊裝。b)軸承安裝把緊。c)測量曲軸臂距差。3.3.1.4 機架吊裝a)機座水平找好后,方可吊裝機架。b)在吊裝機架之前,主軸瓦要用白布或硬紙遮蓋,以防臟物落入。3.3.1.5 安裝連桿十字頭總成,十字頭軸承蓋缺口處用布蓋好。3.3.1.6 安裝缸體總成。3.3.1.7 安裝活塞
31、總成3.3.1.8 安裝缸蓋、掃氣箱、增壓器、定壓管等其它部件。3.3.2 主機分層吊裝3.3.2.1 主機分兩層吊裝a)機座總成、曲軸飛輪總成、機架總成和連桿十字頭總成為第一層;b)缸體總成、活塞總成和缸蓋總成為第二層。3.3.2.2 主機分三層吊裝a)機座總成、曲軸飛輪總成為第一層;b)機架總成和連桿及十字頭總成為第二層;c)缸體總成、活塞總成和缸蓋總成為第三層。3.4 主機安裝結束后的清潔及保護3.4.1 主機安裝結束后,對主機內部進行一次徹底的清潔,清潔后要向主軸承、推力軸承、十字頭軸承、曲柄銷軸承、十字頭滑塊、油拉管等運動部件加入指定的滑油,避免出現干摩擦。另外機內的機加工面(沒有涂
32、油漆的部位)要涂上適量的滑油。3.4.2 用布條或專用堵條封堵主軸承、曲柄銷軸承的兩側,采取保護袋的方式保護十字頭軸承。3.4.3 整臺主機要用三防布來保護,重要部位也要用三防布來保護。如:增壓器壓氣端、曲拐箱的防爆門等。3.4.4 對主機上的敞口管子要用鐵盲板封堵。3.4.5 曲拐箱的防爆門的緊固螺絲要全部把緊,防止灰塵進入機體內。3.5 主機安裝結束后的設備保養從船臺安裝后到主機串油前,按照有關的保養規程進行。4 軸系排軸找正4.1 排軸條件4.1.1 船舶下水48小時后,方可進行排軸找正。4.1.2 船只處于浮態,螺旋槳近乎半浸于水中。4.2 排軸要求4.2.1 按軸系校中計算書提供的數
33、據排軸、定位主機和軸系。4.2.2 排軸找正時對軸系法蘭間的偏移和曲折設定值允許偏差不大于0.05mm。4.3 對于B&W低速柴油機船上定位4.3.1 艉軸與中間軸法蘭,按軸系校中計算書要求的偏移與曲折值進行找正,見圖9。圖9 艉軸與中間軸法蘭找正示意圖4.3.2 測量主機機座扭曲4.3.2.1 在調整主機使之達到中間軸與主機輸出軸連接法蘭的曲折和偏移值的同時,調整主機機座使其扭曲值0.1mm/m。4.3.2.2 方法是用兩個水平儀放在主機的前后端的位置上,兩個人同時讀數,然后計算出扭曲值,如圖10所示:圖10 主機座扭曲測量示意圖4.3.3 測量主機機座撓度 用特殊琴鋼絲工具測量主機
34、凸輪軸側和排氣側機座撓度(圖11),應符合主機制造廠說明書要求。圖11 用琴鋼絲測量主機座撓度示意圖4.3.4 測量主機曲軸臂距差 主機曲軸臂距差的測量,應注意正確的盤車方向,其數值應參考主機制造廠座臺試驗記錄進行(見圖12)。圖12 主機曲軸臂距差測量示意圖4.3.5 軸系法蘭連接螺栓裝配 按螺栓孔配制螺栓,法蘭螺栓及螺栓孔應打鋼印編號,且螺栓號與螺孔號應一一對應。4.3.5.1 螺栓過盈量為0.01mm0.04mm,采用液氮冷縮裝配4.3.5.2 液壓緊配螺栓嚴格按照安裝說明進行定位并液壓拉緊。4.3.6 測量軸承靜態負荷4.3.6.1 對艉軸管前軸承、中間軸承和主機最后端兩個主軸承進行負
35、荷檢驗。4.3.6.2 各軸承冷態靜負荷值應根據軸系校中計算書確定,允許負荷偏差±20%。4.3.6.3 軸承負荷測量方法(以中間軸承負荷測量為例,參見圖13圖13 軸承靜態負荷測量示意圖圖中,L中間軸承中心至千斤頂和百分表中心的距離,此值須按照軸系校中計算書中規定選取。在軸承規定處設置液壓千斤頂,參見圖14。將液壓千斤頂泵壓,從0開始逐漸泵壓升高,最初負荷即軸的重量完全由軸承來承受,隨著壓力逐漸提高,負荷逐漸從軸承移向千斤頂,當軸完全離開軸承后,油壓繼續升高時,軸的垂直移動和軸負荷之間的關系是直線關系,即斜率為常數,千斤頂卸荷時的關系和測量的程序與頂升時相似。延長頂升和下降直線與橫
36、座標形成兩個交點,這兩點平均值即是軸承真正所承受的負荷,根據測量的頂升和下降的位移和相應壓力值,計算出所測軸承的負荷,參見圖14。DROPRISE圖14 軸承靜態負荷頂升曲線示意圖軸承負荷計算公式:R=100×C×P3×A (N)(4)(4)式中:R軸承負荷,單位:N;A液壓千斤頂活塞面積,單位:cm2;A=D2/4 (cm2) (5)(5)式中:D液壓千斤頂活塞直徑,cm ;C距離修正系數,由設計部門提供;P3頂升油壓與頂降油壓的平均值,單位:MPa;P3 =(P1+ P2)/2 (MPa)(6)(6)式中:P1頂升油壓,上升曲線的直線段延長與X軸的交點,單位:
37、MPa;P2頂降油壓,下降曲線的直線段延長與X軸的交點,單位:MPa。4.3.6.4 軸承靜態負荷及主機機座撓度、扭曲、曲軸拐檔差測量合格后,主機進行研墊或澆注樹脂墊。4.3.7 主機采用鋼質墊片或鑄鐵墊片4.3.7.1 當主機既有焊接墊片又有調整墊片時,在焊接墊片焊接前,檢查焊接墊片與基座接觸面貼合良好,用0.10mm塞尺檢查,插入深度不大于10mm,寬度不大于20mm,不多于2處。主機調整墊片研磨后上下接觸面每25mm×25mm 區域內接觸斑點不少于3點,接觸面積不少于75%,0.05mm塞尺插入深度不大于15mm、寬度不大于20mm,允許2處。4.3.7.2 當基座上僅有調整墊
38、片時,檢查要求同4.3.7.1。4.3.7.3 鑄鐵墊片厚度不小于25mm;鋼質墊片厚度不小于15mm。4.3.8 主機采用環氧樹脂澆注墊片4.3.8.1 當主機墊片為環氧樹脂澆注墊片時,要求環氧樹脂墊片澆注部位打磨清潔干凈,不得有任何油污、銹跡和油漆等。4.3.8.2 澆注前,應考慮主機重量和螺栓預緊力所帶來的壓縮,壓縮量為墊片厚度的0.001倍。4.3.8.3 澆注時,必須確保環氧樹脂的溫度不低于13,最佳溫度在2025。a)澆注后,環境溫度不低于13,最佳溫度在2025,保溫時間48小時。b)48小時后,用試樣進行硬度試驗,巴氏硬度大于35、抗壓強度大于93N/mm2。4.3.8.4 環
39、氧樹脂澆注墊片厚度不小于25mm,最大厚度不超過85mm。4.3.9 主機研墊或澆注樹脂墊片結束后,裝配底腳螺栓。對于主機采用過盈配合形式的螺栓,裝配時采用冷縮裝配法或壓入法裝配,也可采用敲入法。緊固后螺栓頭與基座及螺母與機座之間用0.05mm塞尺不得插入。4.3.10 主機底腳螺栓緊固由中間向兩端前后交替進行緊固主機底腳螺栓(如圖15所示),其數據按主機制造廠說明書進行。圖15 主機底腳螺栓緊固示意圖4.3.11 緊固主機底腳螺栓后,再一次測量艉軸管前軸承、中間軸承和主機最后兩個軸承的靜態負荷。4.4 對于非B&W低速柴油機船上定位4.4.1 主機與軸系按軸系校中計算書要求進行找正。
40、4.4.2 主機與軸系之間進行連接。4.4.3 主機進行研墊或澆注樹脂墊。4.4.4 主機研墊或澆注樹脂墊完工后,按要求緊固主機底腳螺栓,測量中間軸承靜態負荷。4.5 主機往復運動件檢查4.5.1 主機活塞裙部與氣缸套間隙檢查。4.5.2 滑塊與十字頭之間的間隙。4.5.3 滑塊與十字頭導板之間的間隙。4.5.4 側板與十字頭導板之間的間隙。4.6 主機側向拉緊裝置4.6.1 機械式側向拉緊裝置4.6.1.1 船體結構加強必須對位。4.6.1.2 螺栓按照規定力矩緊固。4.6.2 液壓式側向拉緊裝置4.6.2.1 船體結構加強必須對位。4.6.2.2 頂推液壓油缸底座與其基座接觸表面研磨后,每
41、25mm×25mm區域內接觸斑點不少于2個。4.6.2.3 螺栓按照規定力矩緊固。4.6.2.4 油缸工作指針必須調整在工作區域。5 舵裝置安裝5.1 舵桿、舵銷、舵葉車間內加工5.1.1 舵桿與舵機或舵柄的錐度樣板制作5.1.1.1 根據到貨后的舵機或舵柄內孔制作公樣板,公樣板的錐面與舵機或舵柄內孔的錐面要吻合,最大部位的縫隙不得大于0.03mm,縫隙長度應小于30mm。5.1.1.2 在公樣板上劃出舵機錐孔的大端線。5.1.1.3 按公樣板制作母樣板,驗收要求為:樣板應平直,對縫接觸應緊密,0.03mm厚度塞尺檢查,插入距離不大于30mm長度,正反兩面應配合一致。5.1.2 舵銷
42、與舵葉、舵桿與舵葉的錐度樣板制作要求同上。5.1.3 舵桿、舵銷、舵葉的錐體部位按相應的公母樣板加工。5.1.4 舵桿/舵銷錐體部分和舵葉錐孔部位及舵桿錐體與舵機/舵柄錐孔加工時應預留研配量,軸向研配量見表8。 表8 舵桿/舵銷與舵葉錐體及舵桿與舵機/舵柄錐體軸向研配量 mm舵桿/舵銷錐部大端直徑 100100200200300300400400500軸向研配量23344556675.2 舵銷套及舵桿套加工及安裝5.2.1 舵銷套及舵桿套加工5.2.1.1 舵銷及舵桿不銹鋼套裝配過盈量為0.0008d,最小極限為0.0005d ,最大極限為0.001d(d舵銷直徑,mm)。5.2.1.2 舵銷
43、及舵桿鑄銅套裝配過盈量0.0012d,最小極限為0.00075d,最大極限為0.0015d(d舵銷直徑,mm)。5.2.2 舵銷套及舵桿套安裝5.2.2.1 舵銷套及舵桿套采用烘裝方法安裝,烘裝前應對襯套做0.1MPa的密性試驗。5.2.2.2 襯套的內孔按圖紙要求加工成品,外圓留余量,烘裝后再將外圓加工成品。根據襯套的實際內徑制作丁字型量規,對襯套均勻加熱至280320,使其內徑膨脹到1.52mm即可裝配。. 5.3 舵桿、舵銷與舵葉研配 5.3.1 將舵葉平置于平臺或堅固地面上,下面加木墩調好高度和水平。5.3.2 順舵葉長度方向拉兩根鋼絲線,一根在舵銷孔中心線上方,另一根在舵葉一側,用劃
44、在舵葉上的中心線找正調整兩線,使之與舵系中心線基本平行,如圖16所示(帶掌面的舵桿)。圖16 舵系拉線研配示5.3.3 舵桿與舵葉法蘭連接接觸面的研配5.3.3.1 以舵葉法蘭為基準,用塞尺測量舵桿與舵葉法蘭面的間隙以確定舵桿法蘭面的研磨處及研配量。5.3.3.2 舵桿與舵葉連接后的中心線偏差應不大于0.30mm,極限不大于0.50mm。5.3.3.3 舵桿與舵葉法蘭面研磨的質量要求:每25mm×25mm區域內接觸斑點不少于2個,接觸面積不少于60%,沿法蘭周長90%處0.05mm塞尺不得插進,其余處插入深度不大于15mm。5.3.3.4 舵葉與舵桿法蘭連接鉸孔螺栓a)螺栓過盈量為0
45、mm0.02mm。b)鉸孔螺栓與螺栓孔,圓度不大于0.015mm,圓柱度不大于0.02mm。c)采用冷縮法裝配螺栓或用壓入法裝配,壓入力30kN150kN。5.3.4 研配時,參照圖17所示位置進行測量,在舵桿上和舵銷上兩處測得至鋼絲線的尺寸差(千分尺讀數差)應小于0.05mm。5.3.5 舵系研配時,對上方所拉的一根鋼絲線進行測量時,應按公式(1)考慮鋼絲下垂量影響:5.3.6 舵桿與舵葉及舵銷與舵葉錐體連接表面研磨后,接觸面每25mm×25mm區域內接觸斑點不少于2點,接觸面積不得少于70%,0.03mm厚度塞尺在錐度兩端不得塞入。5.3.7 舵系中心線復查舵桿、舵銷與舵葉連接后
46、,中心線偏差應不大于0.30mm,極限不大于0.50mm。5.4 舵桿與舵機或舵柄連接錐面研配5.4.1 確定艏艉方向并做標記。5.4.2 舵桿與舵機或舵柄錐體連接表面研磨后,接觸面每25mm×25mm區域內接觸斑點不少于2點,接觸面積不得少于70%,0.03mm厚度塞尺在錐度兩端不得塞入。5.4.3 舵桿與舵柄(帶鍵結構)5.4.3.1 錐體接觸面每25mm×25mm區域內接觸斑點2點,接觸面積不得少于70%,0.03mm厚度塞尺在錐孔兩端允許局部塞入。5.4.3.2 舵柄鍵槽與鍵研配,側面允許間隙0.04 mm0.06mm,極限0.07mm。5.4.3.3 舵桿與鍵研配
47、,鍵槽兩側0.03mm厚度塞尺不得塞入,槽底著色接觸比應在40%以上,聽聲音不得懸空,鍵頂應有2%鍵高間隙,最大不超過1mm。5.4.3.4 舵柄的壓入量0.5mm1.0mm或人工打緊。5.4.4 舵桿與舵機或舵柄在車間內預裝。5.4.5 舵承與摩擦片研配要求:接觸面50%,間隙0.05mm,見圖17。圖17 舵承結構示意圖5.5 拉舵系中心線5.5.1 按船體交驗合格的上下舵線基準點拉舵系中心線,并制作加工用基準塊(見圖18)。圖18 拉舵系中心線示意圖5.5.2 檢查舵系中心線與軸系中心線偏差,要求同2.1.3.1。5.5.3 各基準塊中心與所拉舵系中心線的距離允差0.03mm。5.5.4
48、 根據設計圖紙給定的舵系中心線至艉軸管成品后端面的垂直距離,確定舵系各軸承孔是否有足夠的加工余量。5.6 舵系軸承孔加工5.6.1 鏜桿某一點為測量點,以基準點或基準圓線為基準找正,調整鏜桿,檢查鏜桿安裝的正確性,允許偏差為±0.03mm。5.6.2 舵系軸承內孔加工精度符合表9要求。表9 舵系軸承內孔加工精度 mm舵系軸承內孔直徑200400400600600800圓度/圓柱度0.030.040.055.6.3 舵承基座或舵機座應在船上焊后加工,其加工后的基座平面對舵線中心之垂直度不大于0.15mm/m。5.6.4 上下各孔加工后中心線徑向偏差不大于L0.30mm,見圖19。圖19
49、 舵系上下各孔加工后徑向偏差示意圖5.7 舵鈕襯套加工要求及安裝5.7.1 鑄銅或不銹鋼襯套,裝配過盈量(0.050.16)mm,壓入力(20500)kN,極限:800kN。5.7.2 非金屬襯套按照制造廠要求進行加工和安裝。5.8 舵系各部件船上安裝5.8.1 按要求對舵桿與舵葉、舵銷與舵葉安裝。5.8.2 舵機安裝5.8.2.1 往復柱塞式(撞桿式)液壓舵機a)鋼質調整墊片接觸面每25mm×25mm區域內接觸斑點2點以上,接觸面積不得少于60%,0.05mm厚度塞尺允許局部塞入深度不超過15mm,寬度不超過20mmb)檢查各油缸柱塞在油缸中的間隙,水平方向上允差不大于0.07mm
50、,底部不得有間隙c)檢查舵機各對角線距離應相等,允差1mm,參見圖20。a=b=c=d 圖20 舵機對角線檢查示意圖d)舵機與舵柄安裝平行度檢查,允差0.05mm,參見圖21。 圖21 舵機舵柄平行度測量示意圖 5.8.2.2 轉葉式液壓舵機 a)舵機和舵桿按要求進行壓裝b)舵系進行找正,各部軸承進行調整。c)舵機采用等厚墊,墊片經過磨削后可直接安裝在舵機下面,用0.05mm厚度的塞尺檢查允許局部塞入,深度不超過10mm,寬度不超過15mm。d)舵機底座采用環氧樹脂澆注墊片時,其要求按4.3.8,僅墊片厚度應不小于13mm5.8.3 舵止跳塊安裝安裝位置和安裝間隙根據圖紙和廠家說明書要求進行。
51、5.8.4 舵零位校正在船臺/船塢中線與船中線保持一致的情況下,將船中線向后延長超過舵葉,再由舵尖邊緣中部吊重錘到船臺/船塢中線,穩定在±5mm范圍內。5.8.5 轉舵試驗左右轉舵至最大設計角度,確定在操舵范圍內不得與掛舵臂相碰,檢查其靈活性。5.8.6 船下水前,封固舵系。6 主柴油發電機組安裝6.1 上船前應在車間對柴油機曲軸臂距差檢查一次,并做好記錄。6.2 對船上發電機組的基座,應按發電機組安裝圖進行檢查,確保布置位置及尺寸的正確性。6.3 發電機基座螺栓孔應按發電機機座號孔或按機做樣板號孔,要求準確可靠。6.4 不帶減振墊的柴油發電機組船上安裝6.4.1 基座面板及焊接墊片6.4.1.1 焊接墊片與基座應緊密貼合,焊固后不得中空。6.4.1.2 接觸面每25mm×25mm區域內接觸斑點2點以上,接觸面積不得少于60%,0.05mm塞尺允許局部塞入深度不大于10mm,寬度不大于15mm,允許一處。6.4.1.3 焊接墊片上平面1:100斜度朝外。6.4.2 調整墊研配6.4.2.1 發電機落座在基座上后,進行調整,測量曲軸拐擋差值符合要求,然后研配調整墊。6.4.2.2 墊接觸面每25mm×25mm區域內接觸斑點2點以上,接觸面積不得少于60%,0.05mm塞尺
溫馨提示
- 1. 本站所有資源如無特殊說明,都需要本地電腦安裝OFFICE2007和PDF閱讀器。圖紙軟件為CAD,CAXA,PROE,UG,SolidWorks等.壓縮文件請下載最新的WinRAR軟件解壓。
- 2. 本站的文檔不包含任何第三方提供的附件圖紙等,如果需要附件,請聯系上傳者。文件的所有權益歸上傳用戶所有。
- 3. 本站RAR壓縮包中若帶圖紙,網頁內容里面會有圖紙預覽,若沒有圖紙預覽就沒有圖紙。
- 4. 未經權益所有人同意不得將文件中的內容挪作商業或盈利用途。
- 5. 人人文庫網僅提供信息存儲空間,僅對用戶上傳內容的表現方式做保護處理,對用戶上傳分享的文檔內容本身不做任何修改或編輯,并不能對任何下載內容負責。
- 6. 下載文件中如有侵權或不適當內容,請與我們聯系,我們立即糾正。
- 7. 本站不保證下載資源的準確性、安全性和完整性, 同時也不承擔用戶因使用這些下載資源對自己和他人造成任何形式的傷害或損失。
最新文檔
- 2025用人單位終止勞動合同應當承擔的賠償責任
- 中藥吳鵬桔梗
- 2025版設計合同樣本
- 園來如此-園林規劃設計知到課后答案智慧樹章節測試答案2025年春云南林業職業技術學院
- 2025年南京房屋租賃合同
- 片石購銷合同范本
- 2025員工試用期間勞動合同樣本
- 2025年土地使用權轉讓合同樣本
- 2024年南通市崇川區教育系統招聘教師真題
- 2024年懷化市產業投資集團有限公司招聘真題
- 大學國旗護衛班培訓方案
- 胃腸術后吻合口瘺的觀察與護理
- 圓柱的認識說課演示稿
- 足療店應急處理預案方案
- 產后出血預防與處理策略
- (完整word版)勞動合同書(電子版)正規范本(通用版)
- 人教版五年級下冊數學期末質量檢測試卷含答案
- 成品可靠性測試計劃
- 2022版數學課程標準解讀
- 金屬廢品回收合同
- 鋁合金門窗施工組織設計方案
評論
0/150
提交評論