
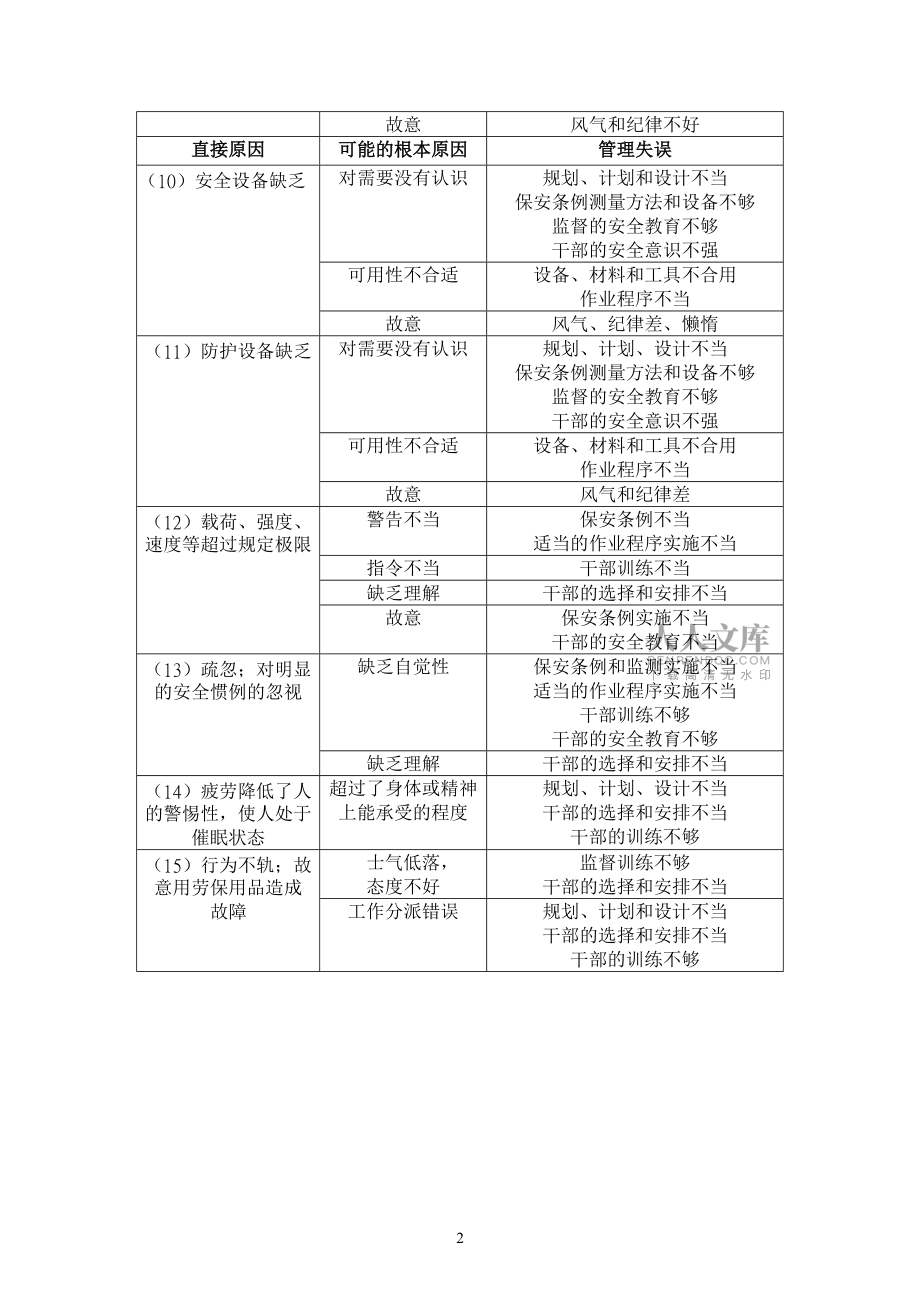



版權(quán)說明:本文檔由用戶提供并上傳,收益歸屬內(nèi)容提供方,若內(nèi)容存在侵權(quán),請進行舉報或認領(lǐng)
文檔簡介
1、失效分析的思路與診斷第二章 失效分析的思路第一節(jié) 常用的幾種失效分析思路一、“撤大網(wǎng)”逐個因素排除法表2-1 事故的管理責任直接原因可能的根本原因管理失誤(1)輔助工作太差對危險不認識監(jiān)督訓(xùn)練和安全教育不夠設(shè)施不當規(guī)劃、計劃不當(2)使用的工具、裝置和設(shè)施不適當缺乏知識和技能干部的訓(xùn)練不夠缺乏適當?shù)淖鳂I(yè)程序確定的操作程序不合適缺乏自覺性監(jiān)督安全教育不夠適合的作業(yè)程序?qū)嵤┎划敻刹康挠?xùn)練和安全措施不夠(3)裝置和設(shè)施不安全或有毛病對不安全不認識監(jiān)督安全教育不夠干部對訓(xùn)練和安全重視不夠設(shè)計或選擇太差規(guī)劃、計劃、設(shè)計不當監(jiān)督安全教育不夠裝置、材料或工具不合適維護太差維護和修理體系不當(4)缺乏適當?shù)淖?/p>
2、業(yè)程序省略作業(yè)程序操作程序不妥設(shè)計者的錯誤規(guī)劃、計劃、設(shè)計不當監(jiān)督者的錯誤監(jiān)督不熟練(5)臨時湊合的不安全作業(yè)程序訓(xùn)練不當確定的操作程序不當合適的作業(yè)程序?qū)嵤┎划敱O(jiān)督的安全教育不夠干部的訓(xùn)練和安全教育不夠監(jiān)督不當監(jiān)督的安全教育不夠干部的選擇和安排不當(6)沒有按規(guī)定的作業(yè)程序?qū)嵤π枰獩]強調(diào)合適的作業(yè)程序?qū)嵤┎划敱O(jiān)督的安全教育不夠作業(yè)程序不清楚操作程序不當(7)對工作不了解指令復(fù)雜操作程序、規(guī)劃、計劃和設(shè)計不當理解不夠干部的選擇和安排不當(8)沒有意識到危險指令不當監(jiān)督的安全教育不夠干部的訓(xùn)練和安全教育不夠警告不當規(guī)劃、計劃、設(shè)計不當保安條例、測量方法和設(shè)備不當操作程序不當(9)缺乏適當?shù)墓ぞ?/p>
3、、裝置和設(shè)施對需要沒認識規(guī)劃、計劃、設(shè)計不當監(jiān)督的安全教育不夠供應(yīng)不當設(shè)備、材料和工具不夠或不當故意風氣和紀律不好直接原因可能的根本原因管理失誤(10)安全設(shè)備缺乏對需要沒有認識規(guī)劃、計劃和設(shè)計不當保安條例測量方法和設(shè)備不夠監(jiān)督的安全教育不夠干部的安全意識不強可用性不合適設(shè)備、材料和工具不合用作業(yè)程序不當故意風氣、紀律差、懶惰(11)防護設(shè)備缺乏對需要沒有認識規(guī)劃、計劃、設(shè)計不當保安條例測量方法和設(shè)備不夠監(jiān)督的安全教育不夠干部的安全意識不強可用性不合適設(shè)備、材料和工具不合用作業(yè)程序不當故意風氣和紀律差(12)載荷、強度、速度等超過規(guī)定極限警告不當保安條例不當適當?shù)淖鳂I(yè)程序?qū)嵤┎划斨噶畈划敻刹坑?xùn)
4、練不當缺乏理解干部的選擇和安排不當故意保安條例實施不當干部的安全教育不當(13)疏忽;對明顯的安全慣例的忽視缺乏自覺性保安條例和監(jiān)測實施不當適當?shù)淖鳂I(yè)程序?qū)嵤┎划敻刹坑?xùn)練不夠干部的安全教育不夠缺乏理解干部的選擇和安排不當(14)疲勞降低了人的警惕性,使人處于催眠狀態(tài)超過了身體或精神上能承受的程度規(guī)劃、計劃、設(shè)計不當干部的選擇和安排不當干部的訓(xùn)練不夠(15)行為不軌;故意用勞保用品造成故障 士氣低落,態(tài)度不好監(jiān)督訓(xùn)練不夠干部的選擇和安排不當工作分派錯誤規(guī)劃、計劃和設(shè)計不當干部的選擇和安排不當干部的訓(xùn)練不夠二、以設(shè)備制造全過程為一系統(tǒng)進行分析 任何一個設(shè)備都要經(jīng)歷規(guī)劃、設(shè)計、選材、機械加工(包括鑄
5、、鍛、焊等工藝)、熱處理、二次精加工(研磨、酸洗、電鍍)和裝配等制作工序,如果失效已確定純屬設(shè)備問題,還可對上述工序逐個進一步分析,包括以下內(nèi)容:1. 設(shè)計不當(1) 開孔位置不當造成應(yīng)力集中;(2) 缺口或凹倒角半徑過小;(3) 高應(yīng)力區(qū)有缺口;(4) 橫截面改變太陡;(5) 改變設(shè)計,沒有相應(yīng)地改變受力狀況;(6) 設(shè)計判據(jù)不足;(7) 計算中出現(xiàn)過載荷;(8) 焊縫選擇位置不當,以及配合不適當?shù)龋唬?) 對使用條件的環(huán)境影響,未做適當考慮;(10) 提高使用材料的受力級別;(11) 剛性和韌性不適當;(12) 材料品種選擇錯誤;(13) 選擇標準不當;(14) 材料性能數(shù)據(jù)不全;(15)
6、 材料韌脆轉(zhuǎn)變溫度過高;(16) 對現(xiàn)場調(diào)查不充分,認識不足就投入設(shè)計;(17) 與用戶配合有差錯。2. 材料、冶金缺陷(1) 成分不合格;(2) 夾雜物含量及成分不合格;(3) 織組不合格;(4) 各種性能不合格;(5) 各向異性不合格;(6) 斷口不合格;(7) 冶金缺陷(縮孔、偏析等);(8) 惡化變質(zhì);(9) 混料。3. 鍛造等熱加工工藝缺陷(1) 折疊、夾砂、夾渣;(2) 裂縫;(3) 鍛造鱗皮;(4) 流線分布突變或破壞;(5) 晶粒流變異常;(6) 沿晶氧化(過燒);(7) 氧化皮壓入;(8) 分層、疏松;(9) 帶狀組織;(10) 過熱、燒裂;(11) 外來金屬夾雜物;(12)
7、 縮孔;(13) 龜裂;(14) 打磨裂紋;(15) 皺紋。4. 機械加工缺陷(1) 未按圖紙要求;(2) 表面粗糙度不合格;(3) 倒角尖銳;(4) 磨削裂紋或過燒;(5) 裂紋;(6) 劃傷、刀痕;(7) 毛刺;(8) 局部過熱;(9) 矯直不當。5. 鑄造缺陷(1) 金屬突出;(2) 孔穴;(3) 疏松;(4) 不連貫裂紋;(5) 表面缺陷;(6) 澆注不完全;(7) 尺寸和形狀不正確;(8) 夾砂、夾渣;(9) 組織反常;(10) 型芯撐、內(nèi)冷鐵。6. 焊接缺陷(1) 錯口超標;(2) 咬邊超標;(3) 焊肉過凸或過凹;(4) 焊道深溝;(5) 焊趾、焊縫或根部有裂紋;(6) 熔化不全
8、;(7) 打弧;(8) 焊接深度不夠,未焊透;(9) 夾渣、夾雜或疏松;(10) 接頭尺寸不合格;(11) 熱輸入不適當;(12) 焊前預(yù)熱不足;(13) 焊后消除熱應(yīng)力不夠或未消除;(14) 顯微組織不合格;(15) 焊接裂紋。7. 熱處理不當(1) 過熱或過燒;(2) 顯微組織不合格;(3) 淬火裂紋;(4) 淬火變形、翹曲;(5) 奧氏體化溫度不當使晶粒粗大;(6) 脫碳或增碳;(7) 滲氮;(8) 回火脆化;(9) 淬火后未及時回火;(10) 熱應(yīng)力。8. 再加工缺陷(1) 酸洗后或電鍍后未除氫或除氫不夠;(2) 酸跡清洗未盡;(3) 鍍前噴丸清洗不全;(4) 電鍍電極打弧引起硬點;(
9、5) 鍍Cd、鍍Zn的液態(tài)金屬脆化;(6) 形成金屬間化合物致脆;(7) 碰傷、標記壓痕過深或位置不當;(8) 校直引起殘余應(yīng)力;(9) 鍍鉻碎屑劃傷;(10) 化學(xué)熱處理不當;a. 滲層組織反常;b. 力學(xué)性能不合格。9. 裝配檢驗中的問題(1) 軸線對中不正;(2) 緊固件松動;(3) 敲打損傷;(4) 裝配損傷;(5) 裝配不正確;(6) 強迫裝配;(7) 裝配說明書說明不全或不清楚;(8) 裝配馬虎大意;(9) 磁粉檢查電弧燒傷;(10) 磁化吸住鋼屑造成磨損;(11) 漏檢。10. 使用和維護不當(1) 超載、超溫、超速;(2) 沖撞、熱沖擊;(3) 振動過大的斷續(xù)載荷;(4) 操作
10、錯誤、沒按說明書要求做;(5) 每次開車或停車猛烈、突然;(6) 清洗劑不適合;(7) 潤滑不當;(8) 疏忽,不按期維護;(9) 沒定期檢查;(10) 修理不當;(11) 災(zāi)害預(yù)防措施不完善;(12) 安全措施差;(13) 漏電;(14) 早期疲勞裂紋。11. 環(huán)境損傷(1) 腐蝕性氣氛介質(zhì);(2) 高溫或溫度陡度過大;(3) 低溫;(4) 海洋氣氛;(5) 堿性溶液;(6) 氨氣氛;(7) 潤滑介質(zhì)不適合;(8) 潤滑劑變質(zhì)或污染;(9) 流體介質(zhì)中含有磨粒;(10) 控制的或規(guī)定的環(huán)境不適當。 上面列舉了可能引起設(shè)備系統(tǒng)失效的一些主要因素,當然這并非全部因素。還應(yīng)指出,在某一大方面(如熱
11、處理不當)的因素中,有的還可以往前追查原因,例如對于熱處理不當?shù)拇慊鹆鸭y,還可進一步分析其原因,如表2-2所列舉的。表2-2 導(dǎo)致形成淬火裂紋的因素1.材料因素(1) 原材料已有缺陷a. 宏觀偏析;b.固溶體偏析;c.原有裂紋;d. 嚴重脫碳;e.夾雜嚴重;f.疏松;g.夾渣(2) 原始組織不良a. 晶粒粗大;b.魏氏組織;c.組織應(yīng)力;d. 鍛造流線;e.碳化物帶狀組織;f. 鐵素體-珠光體帶狀組織(3) 軋制缺陷或鍛造缺陷(4) 溶進氫(5) 選材不當2.工藝因素(1) 機加工不良a.印壓痕; b.刀痕(2) 零件外形不合理(3) 沒有預(yù)熱,加熱速度太快(4) 奧氏體化溫度過高(5) 保溫
12、時間過長(6) 表層脫碳(7) 滲碳淬火處理中滲碳量過多(8) 淬火冷卻速度太快(9) 加熱或冷卻不均勻(10) 淬火后未及時回火,容許溫度降得太低(11) 掉入油槽底部,因底部有水淬裂(12) 冷卻介質(zhì)選擇不當對于使用中承受交變載荷的部分出現(xiàn)的早期疲勞斷裂,也可進一步分析其失效原因,如表2-3所示:表2-3 金屬部件疲勞失效的誘發(fā)因素外因1.工作條件(1) 加載頻率a.低周高應(yīng)力; b.頻繁斷續(xù)加載(2) 超轉(zhuǎn)速(3) 工作溫度a.過低或過高; b.波動大(4) 環(huán)境介質(zhì)a.腐蝕性氣氛或介質(zhì);b.堿性清洗劑腐蝕;c.點腐蝕;d.環(huán)境氫;e.潤滑劑不合要求(5) 使用載荷集中(6) 應(yīng)力-時間
13、曲線形狀(7) 非零的平均應(yīng)力2.振蝕(微振磨損)3.累積損傷內(nèi)因1. 材料化學(xué)成分不合格2. 宏觀組織的均勻性不合格3. 金相組織不合格(1) 晶粒粗大或混晶;(2)存在魏氏組織;(3) 帶狀組織嚴重; (4)氧化物夾雜不合格;(5) 皮下碳化物聚集4. 材料內(nèi)部缺陷a.冶煉缺陷; b.鑄造缺陷; c.鍛造缺陷; d.焊接缺陷;5. 熱處理缺陷6. 機加工引起的(包括設(shè)計的)缺陷a.表面加工粗糙; b.表面擦傷、劃傷;c.表面殘余拉應(yīng)力; d.校直不當造成的殘余拉應(yīng)力;e.壓印標記造成的殘余拉應(yīng)力;f.開孔位置錯誤;g.倒角尖銳; h.電弧燒傷應(yīng)力集中;i.焊點應(yīng)力集中; j.外形截面突變?nèi)?/p>
14、、根據(jù)部件失效模式分析 機械產(chǎn)品一旦失效,一般表現(xiàn)為過量變形、表面損傷、破裂或斷裂三種主要形式。這些類型還要進一步按失效模式再細分類。下面表2-4是按實際觀察到的一些失效模型所作的分類。表2-4 金屬零部件的各種失效模式1.過量變形(1)力和溫度或者力或溫度引起彈性變形(2)屈服(3)壓痕(4)蠕變(5)沖擊變形2.表面損傷(1)磨損a.粘著磨損; b.磨粒磨損; c.腐蝕磨損; d. 變形磨損; e.沖擊磨損; f.微振磨損;g. 接觸疲勞磨損; h.剝落(2)腐蝕a. 均勻腐蝕; b.縫隙腐蝕; c.電池作用腐蝕; d. 點腐蝕; e.晶間腐蝕; f.選擇浸出;g. 沖蝕; h.氣蝕; i
15、.氫損傷; j.生物腐蝕;k. 應(yīng)力腐蝕;l.微振腐蝕3.斷裂(1)延性斷裂(2)脆性斷裂(3)沖擊斷裂(4)疲勞斷裂a.高溫疲勞; b.高周疲勞; c.低周疲勞; d. 熱疲勞; e.接觸疲勞; f.沖擊疲勞;g. 腐蝕疲勞; h.微振疲勞(5)應(yīng)力持久斷裂(6)蠕變-疲勞復(fù)合斷裂六、根據(jù)部件和設(shè)備類別分析1. 軸類零件的失效原因軸類的失效模式,有以下12種:(1) 單向彎曲疲勞;(2) 雙向彎曲疲勞;(3) 旋轉(zhuǎn)彎曲疲勞;(4) 扭轉(zhuǎn)疲勞;(5) 接觸疲勞;(6) 微振疲勞;(7) 脆性疲勞;(8) 延性疲勞;(9) 塑性變形;(10) 磨損失效;(11) 蠕變斷裂;(12) 腐蝕斷裂。常
16、見的有彎曲疲勞損壞、扭轉(zhuǎn)疲勞損壞、復(fù)合的(彎曲和扭轉(zhuǎn))疲勞損壞、和超載或撞擊的延性斷裂。引起軸類失效的原因如表2-8和表2-9所示。表2-8 軸類失效的原因與誘發(fā)因素1.設(shè)計不當(1) 應(yīng)力集中(鍵槽端、壓配合鍵端、油孔邊軸肩內(nèi)圓角、內(nèi)角尖銳、橫截面突變)(2) 振動2.材料問題(1) 冶金缺陷(鍛造折疊、皮下缺陷、非金屬夾雜偏聚)(2) 化學(xué)成分或力學(xué)性能與說明書不合(3) 韌-脆轉(zhuǎn)變溫度過高(4) 對氫脆、堿脆、回火脆敏感3.制造缺陷(1) 感應(yīng)加熱裂紋(2) 電火花加工孔邊裂紋(3) 淬火裂紋(4) 加工刀痕,磨削損傷(5) 認別標記4.裝配不當合軸偏心5.維護使用不當(1) 惡劣的作業(yè)
17、條件(2) 不正當使用(沖撞、扭轉(zhuǎn)超載)(3) 砂子和金屬粒子引起的震動、磨損(4) 電腐蝕(5) 修理不當表2-9 聯(lián)邦德國阿利安茨技術(shù)中心19681975年間對傳動軸和支承軸失效案例統(tǒng)計失效原因失效實例分布率,%失效位置失效實例分布率,%產(chǎn)品缺陷 a運行失誤故障 b外界影響 c603010結(jié)構(gòu)上的缺口處有腐蝕的部位其它位置80155a. 包括制訂產(chǎn)品規(guī)劃和設(shè)計的失誤(結(jié)構(gòu)布局不合理、計算錯誤、幾何形狀不合理、選材不當?shù)龋V圃旃に嚭吞幚砉に囁斐傻娜毕荩ㄈ绾附印㈣T造、熱處理、機加工缺陷等),裝配或安裝造成的缺陷,以及混料、用錯料等原因引起的失效。b. 如因振動造成的松動、安全保護裝置失靈,
18、伺服設(shè)施故障、磨損、腐蝕、失效老化等引起的失效。c. 如自然災(zāi)害、異物侵襲、電網(wǎng)超高壓等造成的失效。2. 滑動軸承的失效原因滑動軸承失效的表現(xiàn)形式,常見的是軸瓦上有磨損溝槽、腐蝕斑塊,剝落和麻點。其原因和誘發(fā)因素列于表2-10。表2-10 滑動軸承失效的原因和誘發(fā)因素1.機加工質(zhì)量差(1) 表面精整質(zhì)量差(2) 劃傷(3) 尺寸規(guī)格不穩(wěn)定(4) 尺寸不合格2.灰塵(臟)大的灰塵顆粒被嵌鑲到軟的軸瓦中3.潤滑不良(1) 外部漏油(2) 吸油內(nèi)網(wǎng)堵塞(3) 油泵有缺陷(4) 油路堵塞或泄漏(5) 減壓閥彈簧失效(6) 軸承嚴重磨損(7) 油孔位置不當,沒對正供油孔(8) 燃料滲入變稀(9) 潤滑劑
19、變質(zhì)(10) 粘滯性不合適4.裝配不正確(1) 軸瓦匹配顛倒(2) 軸頸有錐形(3) 軸瓦內(nèi)孔失圓(4) 壓貼過緊或不足(5) 連桿中心線不同軸(6) 不正當壓扁5.連桿中心線不同軸使連桿被弄彎的原因(1) 違反操作規(guī)程,強拖發(fā)動(2) 安裝錯誤(3) 連桿裝入前,隨意放置或挪動粗心6.超載,沖擊加載7.腐蝕(1) 潤滑油中有酸的生成物(2) 潤滑油溫過高(3) 潤滑油選用不當8.漏電3. 滾動軸承的失效原因不同的失效原因造成滾動軸承失效的形式也大不相同,說明于表2-11和表2-12。4. 彈簧的失效原因彈簧失效的主要模式是疲勞斷裂和脆性斷裂。其次是腐蝕斷裂、應(yīng)力腐蝕斷裂、氫脆、黑脆、松弛、變
20、形和磨損。現(xiàn)將彈簧脆斷和疲勞斷裂的原因和影響因素列表于2-13。至于兩種斷裂的特征,橫向平斷口上無貝殼花樣的為脆斷;斜斷口上有貝殼花樣的為疲勞斷。表2-11 滾動軸承失效的原因及其對應(yīng)的損壞形式失效原因具體案例原因與原因?qū)?yīng)的損壞形式1.潤滑油污染(1) 水汽(2) 磨料(3) 外界物質(zhì)(大顆粒塵土,金屬屑)(1) 腐蝕(1)+(2)劃傷、擦傷(2) 發(fā)灰、變色(3) 磨損、起麻點、剝落2.潤滑不正確(1) 完全沒有潤滑油(2) 供油量太少(3) 潤滑油種類不對(4) 潤滑油太多太稠(5) 潤滑油等級或密度不對(6) 間斷供油(1) 過熱軟化(2) 擦傷、咬合(2)、(3)、(5)粗糙化、起麻
21、點、剝落(4)金屬涂抹(7) 保持架破碎(8)3.安裝不正確(1) 預(yù)壓過大(2) 調(diào)整過緊(3) 強裝(4) 外圈與殼體配合過松(5) 軸與軸承內(nèi)孔配合過松(6) 裝配過緊(7) 使用不正確工具(1)、(2)類似潤滑不足引起的損傷(3) 圈開裂(4) 摩擦腐蝕(5) 蠕變磨損(6) 疲勞至剝落(7) 損傷保持架4.拿放保管粗心(1) 錘擊工具(沖子)敲裝(2) 手錘敲擊座圈(3) 沖頭挖傷油封(4) 保管粗心摔傷(5) 保管或安裝時裝擊成凹坑(1) 外環(huán)出現(xiàn)缺口(2) 裂紋(3) 損壞保持架(4) 引起早期疲勞斷裂(5) 外圈刻裂5.中心洗線失調(diào)(1) 軸彎曲(2) 軸承與軸承座之間夾有外界
22、物質(zhì)(3) 軸向游隙過大(1) 磨損、早期疲勞斷裂(2) 磨損、早期疲勞斷裂(3) 內(nèi)圈內(nèi)孔一側(cè)嚴重磨損6.繁重作業(yè)(1) 短時期內(nèi)特別沉重的沖擊載荷(2) 軸向游隙大加上下振動(3) 速度和載荷過大(4) 振動使?jié)L動體在不動的座圈上前后滑動(1) 座圈壓痕,座圈和滾動體破裂(2) 座圈破碎(3) 座圈表面片狀剝落(4) 凹溝痕跡7.振動磨損加撞擊壓坑8.漏電電麻坑表2-12 滑動軸承和滾動軸承失效案例原因的統(tǒng)計分布失效原因損壞案例的分布率. %滾動軸承(1400例)滾動軸承(530例)1. 產(chǎn)品失效(1) 質(zhì)量低劣(2) 計劃、設(shè)計和計算的錯誤及工藝缺陷(3) 軸承各部件材料使用不當2. 運
23、行失誤(1) 操作失誤、維護不當和監(jiān)控裝置失效(2) 連續(xù)運行中磨損3. 外界影響 (例如在異常情況下運行造成的損壞)30.114.413.81.965.937.428.54.04.023.410.79.13.669.639.130.57.07.0表2-13 彈簧脆性斷裂和疲勞斷裂的原因斷裂模式斷裂原因及影響因素1.脆性斷裂(1)材料缺陷表面缺陷a. 表面裂紋b. 冷拔或冷繞留下的折疊或刻痕c. 磨光鋼絲的橫向磨痕、麻點碰傷表面脫碳內(nèi)部缺陷a. 粗大夾雜b. 層狀結(jié)構(gòu)c. 晶粒異常粗大d. 馬氏體脆性相(2)制造及熱處理方法不當a. 成形不當b. 機加工不當c. 組織不正常d. 過熱或過燒e.
24、 淬火裂紋f. 電鍍不當g. 其它工藝不當(如除氫不盡)2.疲勞斷裂(1)材料缺陷a. 化學(xué)成分不當b. 魏氏組織c. 表面缺口d. 橫向微裂紋e. 小孔f. 皺皮g. 折迭h. 麻坑i. 分層j. 皮下碳化物(2)設(shè)計不當a. 彈簧指數(shù)和硬度配合不當b. 截面尺寸小c. 轉(zhuǎn)速過高,應(yīng)力循環(huán)快(3)制造工藝不當a. 拉拔過度引起撕裂b. 工具傷痕c. 尖銳彎曲d. 繞簧刻痕或裂紋e. 焊接缺陷f. 表面脫碳g. 酸洗電鍍除氫不盡h. 表面噴丸不當i. 店觸點、加熱過熱、電弧坑(4)維護操作不當a. 沖擊載荷頻繁b. 載荷偏心c. 過載d. 腐蝕、微振腐蝕e. 溫度過高或過低f. 磨損5. 齒輪的失效原因 齒輪損傷的模式,主要表現(xiàn)為斷齒和齒面損傷。現(xiàn)將齒輪失效模式和失效原因列表如下。表2-14 齒輪失效的模式、形貌和原因失效模式損傷形貌導(dǎo)致失效原因齒斷裂強制斷裂(1) 脆性斷
溫馨提示
- 1. 本站所有資源如無特殊說明,都需要本地電腦安裝OFFICE2007和PDF閱讀器。圖紙軟件為CAD,CAXA,PROE,UG,SolidWorks等.壓縮文件請下載最新的WinRAR軟件解壓。
- 2. 本站的文檔不包含任何第三方提供的附件圖紙等,如果需要附件,請聯(lián)系上傳者。文件的所有權(quán)益歸上傳用戶所有。
- 3. 本站RAR壓縮包中若帶圖紙,網(wǎng)頁內(nèi)容里面會有圖紙預(yù)覽,若沒有圖紙預(yù)覽就沒有圖紙。
- 4. 未經(jīng)權(quán)益所有人同意不得將文件中的內(nèi)容挪作商業(yè)或盈利用途。
- 5. 人人文庫網(wǎng)僅提供信息存儲空間,僅對用戶上傳內(nèi)容的表現(xiàn)方式做保護處理,對用戶上傳分享的文檔內(nèi)容本身不做任何修改或編輯,并不能對任何下載內(nèi)容負責。
- 6. 下載文件中如有侵權(quán)或不適當內(nèi)容,請與我們聯(lián)系,我們立即糾正。
- 7. 本站不保證下載資源的準確性、安全性和完整性, 同時也不承擔用戶因使用這些下載資源對自己和他人造成任何形式的傷害或損失。
最新文檔
- 山東省棗莊市嶧城區(qū)第二十八中學(xué)2024-2025學(xué)年初三第二次綜合練習生物試題含解析
- 內(nèi)江職業(yè)技術(shù)學(xué)院《會計專業(yè)英語》2023-2024學(xué)年第二學(xué)期期末試卷
- 運城幼兒師范高等專科學(xué)校《能源與動力技術(shù)進展》2023-2024學(xué)年第二學(xué)期期末試卷
- 山東省棗莊市市中學(xué)區(qū)五校聯(lián)考2025屆初三第一次模擬考試(1月)語文試題試卷含解析
- 華北理工大學(xué)輕工學(xué)院《大學(xué)物理學(xué)下》2023-2024學(xué)年第一學(xué)期期末試卷
- 重慶機電職業(yè)技術(shù)大學(xué)《心理咨詢理論與技術(shù)(一)》2023-2024學(xué)年第一學(xué)期期末試卷
- 江西省吉安市吉安縣重點中學(xué)2025屆初三第三次模擬練習英語試題文試題含答案
- 云南能源職業(yè)技術(shù)學(xué)院《鍵盤基礎(chǔ)訓(xùn)練(二)》2023-2024學(xué)年第二學(xué)期期末試卷
- 山東省臨沂市蘭陵縣東苑高級中學(xué)2025屆高三第二次模擬考試物理試題含解析
- 遼寧城市建設(shè)職業(yè)技術(shù)學(xué)院《鍋爐壓力容器安全課程設(shè)計》2023-2024學(xué)年第二學(xué)期期末試卷
- 對患者入院評估的系統(tǒng)化方法試題及答案
- 大小便觀察與護理
- 七年級英語下學(xué)期期中押題預(yù)測卷(深圳專用)(原卷版)
- 2024年貴州貴州路橋集團有限公司招聘真題
- 2025年-重慶市安全員-A證考試題庫附答案
- DB11-T 2397-2025 取水供水用水排水數(shù)據(jù)庫表結(jié)構(gòu)
- 氣相色譜-質(zhì)譜聯(lián)用GC-MS
- 腫瘤患者的血栓預(yù)防及護理
- 作風建設(shè)方面?zhèn)€人簡短總結(jié)
- 職業(yè)病危害告知書
- 幼兒園大班古詩《游子吟》.ppt
評論
0/150
提交評論