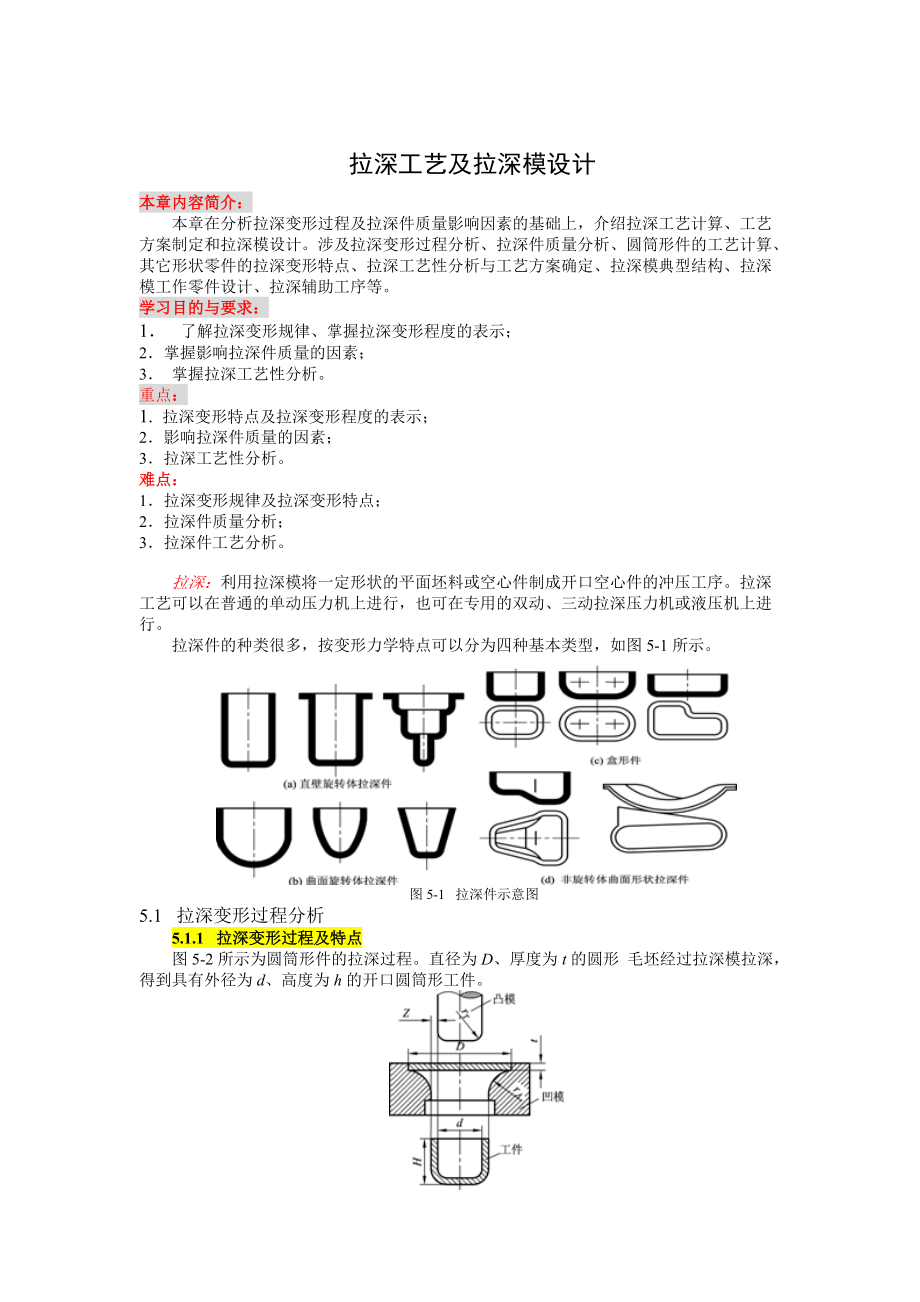




版權說明:本文檔由用戶提供并上傳,收益歸屬內容提供方,若內容存在侵權,請進行舉報或認領
文檔簡介
1、. 拉深工藝及拉深模設計本章內容簡介:本章在分析拉深變形過程及拉深件質量影響因素的基礎上,介紹拉深工藝計算、工藝方案制定和拉深模設計。涉及拉深變形過程分析、拉深件質量分析、圓筒形件的工藝計算、其它形狀零件的拉深變形特點、拉深工藝性分析與工藝方案確定、拉深模典型結構、拉深模工作零件設計、拉深輔助工序等。學習目的與要求:1 了解拉深變形規律、掌握拉深變形程度的表示;2掌握影響拉深件質量的因素;3 掌握拉深工藝性分析。重點:1. 拉深變形特點及拉深變形程度的表示; 2影響拉深件質量的因素;3拉深工藝性分析。難點:1拉深變形規律及拉深變形特點;2拉深件質量分析;3拉深件工藝分析。拉深:利用拉深模將一定
2、形狀的平面坯料或空心件制成開口空心件的沖壓工序。拉深工藝可以在普通的單動壓力機上進行,也可在專用的雙動、三動拉深壓力機或液壓機上進行。拉深件的種類很多,按變形力學特點可以分為四種基本類型,如圖5-1所示。圖5-1 拉深件示意圖5.1 拉深變形過程分析5.1.1 拉深變形過程及特點圖5-2所示為圓筒形件的拉深過程。直徑為D、厚度為t的圓形 毛坯經過拉深模拉深,得到具有外徑為d、高度為h的開口圓筒形工件。圖5-2 圓筒形件的拉深1 在拉深過程中,坯料的中心部分成為筒形件的底部,基本不變形,是不變形區,坯料的凸緣部分(即D-d的環形部分)是主要變形區。拉深過程實質上就是將坯料的凸緣部分材料逐漸轉移到
3、筒壁的過程。2 在轉移過程中,凸緣部分材料由于拉深力的作用,徑向產生拉應力,切向產生壓應力。在和的共同作用下,凸緣部分金屬材料產生塑性變形,其“多余的三角形”材料沿徑向伸長,切向壓縮,且不斷被拉入凹模中變為筒壁,成為圓筒形開口空心件。3圓筒形件拉深的變形程度,通常以筒形件直徑d與坯料直徑D的比值來表示,即m=d/D (5-1)其中m稱為拉深系數,m越小,拉深變形程度越大;相反,m越大,拉深變形程度就越小。5.1.2 拉深過程中坯料內的應力與應變狀態拉深過程是一個復雜的塑性變形過程,其變形區比較大,金屬流動大,拉深過程中容易發生凸緣變形區的起皺和傳力區的拉裂而使工件報廢。因此,有必要分析拉深時的
4、應力、應變狀態,從而找出產生起皺、拉裂的根本原因,在設計模具和制訂沖壓工藝時引起注意,以提高拉深件的質量。根據應力應變的狀態不同,可將拉深坯料劃分為凸緣平面區、凸緣圓角區、筒壁區、筒底圓角區、筒底區等五個區域。1凸緣平面部分(A區) 這是拉深的主要變形區,材料在徑向拉應力和切向壓應力的共同作用下產生切向壓縮與徑向伸長變形而被逐漸拉人凹模。在厚度方向,由于壓料圈的作用,產生了壓應力,但通常和的絕對值比大得多。厚度方向的變形決定于徑向拉應力和切向壓應力之間的比例關系,一般板料厚度有所增厚,越接近外緣,增厚越多。如果不壓料(0),或壓料力較小(小),這時板料增厚比較大。當拉深變形程度較大,板料又比較
5、薄時,則在坯料的凸緣部分,特別是外緣部分,在切向壓應力作用下可能失穩而拱起,形成所謂起皺。圖5-3 拉深過程的應力與應變狀態2凸緣圓角部分(B區)這是位于凹模圓角部分的材料,徑向受拉應力而伸長,切向受壓應力而壓縮,厚度方向受到凹模圓角的壓力和彎曲作用產生壓應力。由于這里切向壓應力值不大,而徑向拉應力最大,且凹模圓角越小,由彎曲引起的拉應力越大,板料厚度有所減薄,所以有可能出現破裂。3筒壁部分(C區) 這部分材料已經形成筒形,材料不再發生大的變形。但是,在拉深過程中,凸模的拉深力要經由筒壁傳遞到凸緣區,因此它承受單向拉應力1的作用,發生少量的縱向伸長變形和厚度減薄。4底部圓角部分(D區) 這是與
6、凸模圓角接觸的部分,它從拉深開始一直承受徑向拉應力和切向拉應力的作用,并且受到凸模圓角的壓力和彎曲作用,因而這部分材料變薄最嚴重,尤其與側壁相切的部位,所以此處最容易出現拉裂,是拉深的“危險斷面”。5筒底部分(E區) 筒底區在拉深開始時即被拉入凹模,并在拉深的整個過程中保持其平面形狀。它受切向和徑向的雙向拉應力作用,變形是雙向拉伸變形,厚度弱有減薄。但這個區域的材料由于受到與凸模接觸面的摩擦阻力約束,基本上不產生塑性變形或者只產生不大的塑性變形。上述筒壁區、底部圓角區和筒底區這三個部分的主要作用是傳遞拉深力,即把凸模的作用力傳遞到變形區凸緣部分,使之產生足以引起拉深變形的經向拉應力1,因而又叫
7、傳力區。5.1.3 拉深件的主要質量問題及控制生產中可能出現的拉深件質量問題較多,但主要的是起皺和拉裂。1起皺 拉深時坯料凸緣區出現波紋狀的皺折稱為起皺。起皺是一種受壓失穩現象。(1) 起皺產生的原因 凸緣部分是拉深過程中的主要變形區,而該變形區受最大切向壓應力作用,其主要變形是切向壓縮變形。當切向壓應力較大而坯料的相對厚度t/D(t為料厚,D為坯料)又較小時,凸緣部分的料厚與切向壓應力之間失去了應有的比例關系,從而在凸緣的整個周圍產生波浪形的連續彎曲,如圖5-4a所示,這就是拉深時的起皺現象。通常起皺首先從凸緣外緣發生,因為這里的切向壓應力絕對值最大。出現輕微起皺時,凸緣區板料仍有可能全部拉
8、入凹模內,但起皺部位的波峰在凸模與凹模之間受到強烈擠壓,從而在拉深件側壁靠上部位將出現條狀的擠光痕跡和明顯的波紋,影響工件的外觀質量與尺寸精度,如圖5-4b所示。起皺嚴重時,拉深便無法順利進行,這時起皺部位相當于板厚增加了許多,因而不能在凸模與凹模之間順利通過,并使徑向拉應力急劇增大,繼續拉深時將會在危險斷面處拉破,如圖5-4c所示。圖5-4 拉深件的起皺破壞(2) 影響起皺的主要因素 坯料的相對厚度t/D 坯料的相對厚度越小,拉深變形區抵抗失穩的能力越差,因而就越容易起皺。相反,坯料相對厚度越大,越不容易起皺。 拉深系數m 根據拉深系數的定義m=d/D可知,拉深系數m越小,拉深變形程度越大,
9、拉深變形區內金屬的硬化程度也越高,因而切向壓應力相應增大。另一方面,拉深系數越小,凸緣變形區的寬度相對越大,其抵抗失穩的能力就越小,因而越容易起皺。有時,雖然坯料的相對厚度較小,但當拉深系數較大時,拉深時也不會起皺。例如,拉深高度很小的淺拉深件時,即屬于這一種情況。這說明,在上述兩個主要影響因素中,拉深系數的影響顯得更為重要。 拉深模工作部分的幾何形狀與參數 凸模和凹模圓角及凸、凹模之間的間隙過大時,則坯料容易起皺。用錐形凹模拉深的坯料與用普通平端面凹模拉深的坯料相比,前者不容易起皺,如圖5-5所示。其原因是用錐形凹模拉深時,坯料形成的曲面過渡形狀(圖5-5b)比平面形狀具有更大的抗壓失穩能力
10、。而且,凹模圓角處對坯料造成的摩擦阻力和彎曲變形的阻力都減到了最低限度,凹模錐面對坯料變形區的作用力也有助于使它產生切向壓縮變形,因此,其拉深力比平端面凸模要小得多,拉深系數可以大為減小。圖5-5 錐形凹模的拉深(3) 控制起皺的措施 為了防止起皺,最常用的方法是在拉深模具上設置壓料裝置,使坯料凸緣區夾在凹模平面與壓料圈之間通過,如圖5-6所示。當然并不是任何情況下都會發生起皺現象,當變形程度較小、坯料相對厚度較大時,一般不會起皺,這時就可不必采用壓料裝置。判斷要否采用壓料裝置可查表確定。圖5-6 帶壓料圈的模具結構2拉裂(1) 拉裂產生的原因 在拉深過程中,由于凸緣變形區應力應變很不均勻,靠
11、近外邊緣的坯料壓應力大于拉應力,其壓應變為最大主應變,坯料有所增厚;而靠近凹模孔口的坯料拉應力大于壓應力,其拉應變為最大主應變,坯料有所變薄。因而,當凸緣區轉化為筒壁后,拉深件的壁厚就不均勻,口部壁厚增大,底部壁厚減小,壁部與底部圓角相切處變薄最嚴重(見圖5-4)。變薄最嚴重的部位成為拉深時的危險斷面,當筒壁的最大拉應力超過了該危險斷面材料的抗拉強度時,便會產生拉裂,如圖5-7所示。另外,當凸緣區起皺時,坯料難以或不能通過凸、凹模間隙,使得筒壁拉應力急劇增大,也會導致拉裂(見圖5-4c)。圖5-7 拉深件的拉裂破壞(2) 控制拉裂的措施 生產實際中常用適當加大凸、凹模圓角半徑、降低拉深力、增加
12、拉深次數、在壓料圈底部和凹模上涂潤滑劑等方法來避免拉裂的產生。5.2 拉深件的工藝性5.2.1 拉深件的形狀、尺寸及精度1. 拉深件的形狀與尺寸(1) 拉深件應盡量簡單、對稱,并能一次拉深成形。(2) 拉深件壁厚公差或變薄量要求一般不應超出拉深工藝壁厚變化規律。根據統計,不變薄拉深工藝的筒壁最大增厚量約為(0.20.3)t,最大變薄量約為(0.10.18)t(t為板料厚度)。(3) 當零件一次拉深的變形程度過大時,為避免拉裂,需采用多次拉深,這時在保證必要的表面質量前提下,應允許內、外表面存在拉深過程中可能產生的痕跡。(4) 在保證裝配要求的前提下,應允許拉深件側壁有一定的斜度。(5) 拉深件
13、的底部或凸緣上有孔時,孔邊到側壁的距離應滿足aR+0.5t(或r+0.5t),如圖5-8a所示。(6) 拉深件的底與壁、凸緣與壁、矩形件的四角等處的圓角半徑應滿足:rt,R2t,rg3t,如圖5-8所示。否則,應增加整形工序。一次整形的,圓角半徑可取r(0.10.3)t,R(0.10.3)t。圖5-8 拉深件的孔邊距及圓角半徑(7) 拉深件的徑向尺寸應只標注外形尺寸或內形尺寸,而不能同時標注內、外形尺寸。帶臺階的拉深件,其高度方向的尺寸標注一般應以拉深件底部為基準,如圖5-9a所示。若以上部為基準(圖5-9b),高度尺寸不易保證。圖5-9 帶臺階拉深件的尺寸標注2. 拉深件的精度一般情況下,拉
14、深件的尺寸精度應在IT13級以下,不宜高于IT11級。對于精度要求高的拉深件,應在拉深后增加整形工序,以提高其精度。由于材料各向異性的影響,拉深件的口部或凸緣外緣一般是不整齊的,出現“突耳”現象,需要增加切邊工序。5.2.2 拉深件的材料用于拉深件的材料,要求具有較好的塑性,屈強比s/b小、板厚方向性系數r大,板平面方向性系數r小。屈強比s/b值越小,一次拉深允許的極限變形程度越大,拉深的性能越好。例如,低碳鋼的屈強比s/b0.57,其一次拉深的最小拉深系數為m=0.480.50;65Mn鋼的s/b0.63,其一次拉深的最小拉深系數為m=0.680.70。所以有關材料標準規定,作為拉深用的鋼板
15、,其屈強比不大于0.66。板厚方向性系數r和板平面方向性系數r反映了材料的各向異性性能。當r較大或r較小時,材料寬度的變形比厚度方向的變形容易,板平面方向性能差異較小,拉深過程中材料不易變薄或拉裂,因而有利于拉深成形。5.3 旋轉體拉深件坯料尺寸的確定5.4 圓筒形件的拉深工藝計算(1)學習目的與要求:1 掌握拉深毛坯形狀與尺寸確定的原則;2 2 掌握旋轉體拉深件坯料尺寸確定的方法;3 3 掌握圓筒形拉深工藝的計算。重點:1。拉深毛坯形狀與尺寸確定的原則;2 圓筒形拉深工藝的計算。難點:圓筒形拉深工藝的計算。5.3 旋轉體拉深件坯料尺寸的確定5.3.1 坯料形狀和尺寸確定的原則1形狀相似性原則
16、 拉深件的坯料形狀一般與拉深件的截面輪廓形狀近似相同,即當拉深件的截面輪廓是圓形、方形或矩形時,相應坯料的形狀應分別為圓形、近似方形或近似矩形。另外,坯料周邊應光滑過渡,以使拉深后得到等高側壁(如果零件要求等高時)或等寬凸緣。2表面積相等原則 對于不變薄拉深,雖然在拉深過程中板料的厚度有增厚也有變薄,但實踐證明,拉深件的平均厚度與坯料厚度相差不大。由于塑性變形前后體積不變,因此,可以按坯料面積等于拉深件表面積的原則確定坯料尺寸。應該指出,用理論計算方法確定坯料尺寸不是絕對準確的,而是近似的,尤其是變形復雜的復雜拉深件。實際生產中,對于形狀復雜的拉深件,通常是先做好拉深模,并以理論計算方法初步確
17、定的坯料進行反復試模修正,直至得到的工件符合要求時,再將符合實際的坯料形狀和尺寸作為制造落料模的依據。由于金屬板料具有板平面方向性和受模具幾何形狀等因素的影響,制成的拉深件口部一般不整齊,尤其是深拉深件。因此在多數情況下還需采取加大工序件高度或凸緣寬度的辦法,拉深后再經過切邊工序以保證零件質量。切邊余量可參考表。但當零件的相對高度H/d很小并且高度尺寸要求不高時,也可以不用切邊工序。5.3.2 簡單旋轉體拉深件坯料尺寸的確定旋轉體拉深件坯料的形狀是圓形,所以坯料尺寸的計算主要是確定坯料直徑。對于簡單旋轉體拉深件,可首先將拉深件劃分為若干個簡單而又便于計算的幾何體,并分別求出各簡單幾何體的表面積
18、,再把各簡單幾何體的表面積相加即為拉深件的總表面積,然后根據表面積相等原則,即可求出坯料直徑。例如,圖5-10所示的圓筒形拉深件,可分解為無底圓筒1、1/4凹圓環2和圓形板3三部分,每一部分的表面積分別為:A1=d(H-r)A2=2r(d-2r)+8r2/4A3=(d-2r)2/4設坯料直徑為D,則按坯料表面積與拉深件表面積相等原則有:D2/4=A1+A2+A3分別將A1、A2、A3代入上式并簡化后得: D= (5-2)式中 D坯料直徑;d、H、r拉深件的直徑、高度、圓角半徑。計算時,拉深件尺寸均按厚度中線尺寸計算,但當板料厚度小于1mm時,也可以按零件圖標注的外形或內形尺寸計算。圖5-10
19、圓筒形拉深件坯料尺寸計算圖常用旋轉體拉深件坯料直徑的計算公式可查表。5.3.3 復雜旋轉體拉深件坯料尺寸的確定復雜旋轉體拉深件是指母線較復雜的旋轉體零件,其母線可能由一段曲線組成,也可能由若干直線段與圓弧段相接組成。復雜旋轉體拉深件的表面積可根據久里金法則求出,即任何形狀的母線繞軸旋轉一周所得到的旋轉體表面積,等于該母線的長度與其形心繞該軸線旋轉所得周長的乘積。如圖5-11所示,旋轉體表面積為 A=2RxL 根據拉深前后表面積相等的原則,坯料直徑可按下式求出: D2/4=2RxL D = (5-3)式中 A旋轉體表面積(mm2);Rx旋轉體母線形心到旋轉軸線的距離(稱旋轉半徑,mm);L旋轉體
20、母線長度(mm);D坯料直徑(mm)。圖5-11 旋轉體表面積計算圖由式(5-3)知,只要知道旋轉體母線長度及其形心的旋轉半徑,就可以求出坯料的直徑。當母線較復雜時,可先將其分成簡單的直線和圓弧,分別求出各直線和圓弧的長度L1、L2、Ln和其形心到旋轉軸的距離Rx1、Rx2、Rxn(直線的形心在其中點,圓弧的長度及形心位置可按表5-7計算),再根據下式進行計算:D = (5-4)例5-1 如圖5-12所示拉深件,板料厚度為1mm,求坯料直徑。解:經計算,各直線段和圓弧長度為:l1=27mm,l2=7.85mm,l3=8mm,l4=8.376mm,l5=12.564mm,l6=8mm,l7=7.
21、85mm,l8=10mm。各直線和圓弧形心的旋轉半徑為:Rx1=13.5mm,Rx2=30.18mm,Rx3=32mm,Rx4=33.384mm,Rx5=39.924mm,Rx6=42mm,Rx7=43.82mm,Rx8=52mm。故坯料直徑為:(mm)圖5-12 用解析法計算坯料直徑5.4 圓筒形件的拉深工藝計算5.4.1 拉深系數及其極限前以述及,圓筒形件的拉深變形程度一般用拉深系數表示。在設計沖壓工藝過程與確定拉深工序的數目時,通常也是用拉深系數作為計算的依據。從廣義上說,圓筒形件的拉深系數m是以每次拉深后的直徑與拉深前的坯料(工序件)直徑之比表示(圖5-13),即第一次拉深系數 第二次
22、拉深系數 第n次拉深系數 總拉深系數表示從坯料直徑D拉深至的總變形程度,即圖5-13 圓筒形件的多次拉深拉深變形程度對凸緣區的徑向拉應力和切向壓應力以及對筒壁傳力區拉應力影響極大,為了防止在拉深過程中產生起皺和拉裂的缺陷,就應減小拉深變形程度(即增大拉深系數),從而減小切向壓應力和徑向拉應力,以減小起皺和破裂的可能性。圖5-14為用同一材料、同一厚度的坯料,在凸、凹模尺寸相同的模具上用逐步加大坯料直徑(即逐步減小拉深系數)的辦法進行試驗的情況。其中,圖a表示在無壓料裝置情況下,當坯料尺寸較小時(即拉深系數較大時),拉深能夠順利進行;當坯料直徑加大,使拉深系數減小到一定數值(如m=0.75)時,
23、會出現起皺。如果增加壓料裝置(圖b),則能防止起皺,此時進一步加大坯料直徑、減少拉深系數,拉深還可以順利進行。但當坯料直徑加大到一定數值、拉深系數減少到一定數值(如m=0.50)后,筒壁出現拉裂現象,拉深過程被迫中斷。因此,為了保證拉深工藝的順利進行,就必須使拉深系數大于一定數值,這個一定的數值即為在一定條件下的極限拉深系數,用符號“m”表示。小于這個數值,就會使拉深件起皺、拉裂或嚴重變薄而超差。另外,在多次拉深過程中,由于材料的加工硬化,使得變形抗力不斷增大,所以以后各次極限拉深系數必須逐次遞增,即m1m2m3mn。圖5-14 拉深試驗影響極限拉深系數的因素的因素較多,主要有:(1) 材料的
24、組織與力學性能 一般來說,材料組織均勻、晶粒大小適當、屈強比s/b小、塑性好、板平面方向性系數r小、板厚方向系數r大、硬化指數n大的板料,變形抗力小,筒壁傳力區不容易產生局部嚴重變薄和拉裂,因而拉深性能好,極限拉深系數較小。(2) 板料的相對厚度 t/D 當板料的相對厚度大時,抗失穩能力較強,不易起皺,可以不采用壓料或減少壓料力,從而減少了摩擦損耗,有利于拉深,故極限拉深系數較小。(3) 摩擦與潤滑條件 凹模與壓料圈的工作表面光滑、潤滑條件較好,可以減小拉深系數。 但為避免在拉深過程中凸模與板料或工序件之間產生相對滑移造成危險斷面的過度變薄或拉裂,在不影響拉深件內表面質量和脫模的前提下,凸模工
25、作表面可以比凹模粗糙一些,并避免涂潤滑劑。(4) 模具的幾何參數 模具幾何參數中,影響極限拉深系數的主要是凸、凹模圓角半徑及間隙。凸模圓角半徑rT太小,板料繞凸模彎曲的拉應力增加,易造成局部變薄嚴重,降低危險斷面的強度,因而會降低極限變形程度;凹模圓角半徑rA太小,板料在拉深過程中通過凹模圓角半徑時彎曲阻力增加,增加了筒壁傳力區的拉應力,也會降低極限變形程度;凸、凹模間隙太小,板料會受到太大的擠壓作用和摩擦阻力,增大了拉深力,使極限變形程度減小。因此,為了減小極限拉深系數,凸、凹模圓角半徑及間隙應適當取較大值。但是,凸、凹模圓角半徑和間隙也不宜取得過大,過大的圓角半徑會減小板料與凸模和凹模端面
26、的接觸面積及壓料圈的壓料面積,板料懸空面積增大,容易產生失穩起皺;過大的凸、凹模間隙會影響拉深件的精度,拉深件的錐度和回彈較大。除此以外,影響極限拉深系數的因素還有拉深方法、拉深次數、拉深速度、拉深件形狀等。由于影響因素很多,實際生產中,極限拉深系數的數值一般是在一定的拉深條件下用試驗方法得出的,可查表確定。需要指出的是,在實際生產中,并不是所有情況下都采用極限拉深系數。為了提高工藝穩定性,提高零件質量,必須采用稍大于極限值的拉深系數。5.4.2 圓筒形件的拉深次數與工序尺寸的計算 1. 無凸緣圓筒形件的拉深次數與工序尺寸的計算(1) 拉深次數的確定當拉深件的拉深系數m =d/D大于第一次極限
27、拉深系數m1,即m m1時,則該拉深件只需一次拉深就可拉出,否則就要進行多次拉深。需要多次拉深時,其拉深次數可按以下方法確定: 推算法 先根據t/D和是否壓料條件可查表確定,并查出m1、m2、m3、,然后從第一道工序開始依次算出各次拉深工序件直徑,即d1=m1D、d2=m2d1、dn=mndn-1,直到dnd。即當計算所得直徑dn稍小于或等于拉深件所要求的直徑d時,計算的次數即為拉深的次數。 查表法 圓筒形件的拉深次數還可從各種實用的表格中查取。(2) 各次拉深工序尺寸的計算當圓筒形件需多次拉深時,就必須計算各次拉深的工序件尺寸,以作為設計模具及選擇壓力機的依據。 各次工序件的直徑 當拉深次數
28、確定之后,先從表中查出各次拉深的極限拉深系數,并加以調整后確定各次拉深實際采用的拉深系數。調整的原則是:a) 保證m1 m2 mn=d/D;b) 使m1m1,m2m2,mnmn,且m1m2mn。然后根據調整后的各次拉深系數計算各次工序件直徑:d1=m1Dd2=m2d1dn=mndn-1=d 各次工序件的圓角半徑 工序件的圓角半徑r等于相應拉深凸模的圓角半徑rT,即r=rT。但當料厚t1時,應按中線尺寸計算,這時r=rT+t/2。凸模圓角半徑的確定可參考本章5.8.2。 各次工序件的高度 在各工序件的直徑與圓角半徑確定之后,可根據圓筒形件坯料尺寸計算公式推導出各次工序件高度的計算公式為: (5-
29、5)式中 H1、H2、Hn各次工序件的高度; d1、d2、dn各次工序件的直徑;r1、r2、rn各次工序件的底部圓角半徑;D坯料直徑。 例5-2 計算圖5-15所示圓筒形件的坯料尺寸、拉深系數及各次拉深工序件尺寸。材料為10鋼,板料厚度t=2mm。圖5-15 無凸緣圓筒形件解:因板料厚度t1mm,故按板厚中線尺寸計算。(1) 計算坯料直徑 根據拉深件尺寸,其相對高度為h/d=(76-1)/(30-2)2.7,查表5-4得切邊余量h=6mm。從表5-6中查得坯料直徑計算公式為D=依圖5-15,d=30-2=28mm,r=3+1=4mm,H=76-1+6=81mm,代入上式得D=(mm)(2) 確
30、定拉深次數 根據坯料的相對厚度t/D=2/98.3100%=2%,按表5-1可采用也可不采用壓料圈,但為了保險起見,拉深時采用壓料圈。根據t/D=2%,查表5-8得各次拉深的極限拉深系數為m1=0.50,m2=0.75,m3=0.78,m4=0.80,。故 d1=m1D=0.5098.3=49.2(mm)d2=m2d1=0.7549.2=36.9(mm)d3=m3d2=0.7836.9=28.8(mm)d4=m4d3=0.8028.8=23(mm)因d4=23mm28mm,所以需采用4次拉深成形。(3) 計算各次拉深工序件尺寸 為了使第四次拉深的直徑與零件要求一致,需對極限拉深系數進行調整。調
31、整后取各次拉深的實際拉深系數為m1=0.52,m2= 0.78,m3=0.83,m4=0.846。各次工序件直徑為: d1=m1D=0.5298.3=51.1(mm)d2=m2d1=0.7851.1=39.9(mm)d3=m3d2=0.8339.9=33.1(mm)d4=m4d3=0.84633.1=28(mm)各次工序件底部圓角半徑取以下數值: r1=8mm,r2=5mm ,r3= r4=4mm把各次工序件直徑和底部圓角半徑代入式(5-5),得各次工序件高度為: (mm)(mm)(mm)(mm)以上計算所得工序件尺寸都是中線尺寸,換算成與零件圖相同的標注形式后,所得各工序件的尺寸如圖5-16
32、所示。圖5-16 圓筒形件的各次拉深工序件尺寸5.4 圓筒形件的拉深工藝計算(2)5.5 圓筒形件的拉深力、壓料力與壓料裝置 學習目的與要求:1. 掌握帶凸緣圓筒形件的拉深工藝計算;2 掌握圓筒形件的拉深力和壓料力的計算,拉深時壓力機標稱壓力的選擇;3 熟悉壓料裝置的結構,了解其優缺點。重點:1.帶凸緣圓筒形件的拉深工藝計算;2拉深時壓力機標稱壓力的選擇;3壓料裝置的結構。難點:1.帶凸緣圓筒形件的拉深工藝計算;2拉深時壓力機標稱壓力的選擇;3壓料裝置的結構,優缺點。 2. 帶凸緣圓筒形件的拉深方法與工序尺寸的計算圖5-17所示為帶凸緣圓筒形件及其坯料。通常,當dt/d=1.11.4時,稱為窄
33、凸緣圓筒形件;當dt/d1.4時,稱為寬凸緣圓筒形件。圖5-17 帶凸緣圓筒形件及其坯料帶凸緣圓筒形件的拉深看上去很簡單,好象是拉深無凸緣圓筒形件的中間狀態。但當其各部分尺寸關系不同時,拉深中要解決的問題是不同的,拉深方法也不相同。當拉深件凸緣為非圓形時,在拉深過程中仍需拉出圓形的凸緣,最后再用切邊或其他沖壓加工方法完成工件所需的形狀。(1) 拉深方法 窄凸緣圓筒形件的拉深 窄凸緣圓筒形件是凸緣寬度很小的拉深件,這類零件需多次拉深時,由于凸緣很窄,可先按無凸緣圓筒形件進行拉深,再在最后一次工序用整形的方法壓成所要求的窄凸緣形狀。為了使凸緣容易成形,在拉深的最后兩道工序可采用錐形凹模和錐形壓料圈
34、進行拉深,留出錐形凸緣,這樣整形時可減小凸緣區切向的拉深變形,對防止外緣開裂有利。例如圖5-18所示的窄凸緣圓筒形件,共需三次拉深成形,第一次拉成無凸緣圓筒形工序件,在后兩次拉深時留出錐形凸緣,最后整形達到要求。圖5-18 窄凸緣圓筒形件的拉深第一次拉深 第二次拉深 第三次拉深 成品 寬凸緣圓筒形件的拉深 寬凸緣圓筒形件需多次拉深時,拉深的原則是:第一次拉深就必須使凸緣尺寸等于拉深件的凸緣尺寸(加切邊余量),以后各次拉深時凸緣尺寸保持不變,僅僅依靠筒形部分的材料轉移來達到拉深件尺寸。因為在以后的拉深工序中,即使凸緣部分產生很小的變形,也會使筒壁傳力區產生很大的拉應力,從而使底部危險斷面拉裂。生
35、產實際中,寬凸緣圓筒形件需多次拉深時的拉深方法有兩種法(見圖5-19): a) 通過多次拉深,逐漸縮小筒形部分直徑和增加其高度(圖5-19a)。這種拉深方法就是直接采用圓筒形件的多次拉深方法,通過各次拉深逐次縮小直徑,增加高度,各次拉深的凸緣圓角半徑和底部圓角半徑不變或逐次減小。用這種方法拉成的零件表面質量不高,其直壁和凸緣上保留著圓角彎曲和局部變薄的痕跡,需要在最后增加整形工序,適用于材料較薄、高度大于直徑的中小型帶凸緣圓筒形件。 b) 采用高度不變法(圖5-19b)。即首次拉深盡可能取較大的凸緣圓角半徑和底部圓角半徑,高度基本拉到零件要求的尺寸,以后各次拉深時僅減小圓角半徑和筒形部分直徑,
36、而高度基本不變。這種方法由于拉深過程中變形區材料所受到的折彎較輕,所以拉成的零件表面較光滑,沒有折痕。但它只適用于坯料相對厚度較大、采用大圓角過渡不易起皺的情況。圖5-19 寬凸緣圓筒形件的拉深方法1、2、3、4拉深次序(2) 拉深特點與無凸緣圓筒形件相比,帶凸緣圓筒形件的拉深變形具有如下特點: 帶凸緣圓筒形件不能用拉深系數來反映材料實際的變形程度大小,而必須將拉深高度考慮進去。因為,對于同一坯料直徑D和筒形部分直徑d,可有不同凸緣直徑dt和高度H對應,盡管拉深系數相同(m=d/D),若拉深高度H不同,其變形程度也不同。生產實際中,通常用相對拉深高度H/d來反映其變形程度。 寬凸緣圓筒形件需多
37、次拉深時,第一次拉深必須將凸緣尺寸拉到位,以后各次拉深中,凸緣的尺寸應保持不變。這就要求正確地計算拉深高度和嚴格地控制凸模進入凹模的深度。考慮到在普通壓力機上嚴格控制凸模進入凹模的深度比較困難,生產實踐中通常有意把第一次拉入凹模的材料比最后一次拉入凹模所需的材料增加3%5%(按面積計算),這些多拉入的材料在以后各次拉深中,再逐次擠入凸緣部分,使凸緣變厚。工序間這些材料的重新分配,保證了所要求的凸緣直徑,并使已成形的凸緣不再參與變形,從而避免筒壁拉裂的危險。這一方法對于料厚小于0.5mm的拉深件效果更為顯著。(3) 帶凸緣圓筒形件的拉深變形程度帶凸緣筒件的拉深系數為: mt=d/D (5-6)式
38、中 mt帶凸緣圓筒形件拉深系數;d拉深件筒形部分的直徑;D坯料直徑。當拉深件底部圓角半徑r與凸緣處圓角半徑R相等,即r=R時,坯料直徑為D=所以 mt=d/D= (5-7)由上式可以看出,帶凸緣圓筒形件的拉深系數取決于下列三組有關尺寸的相對比值:凸緣的相對直徑dt/d;零件的相對高度H/d;相對圓角半徑R/d。其中以dt/d影響最大,H/d次之,R/d影響較小。帶凸緣圓筒形件首次拉深的極限拉深系數見表。由表可以看出,dt/d1.1時,極限拉深系數與無凸緣圓筒形件基本相同,dt/d大時,其極限拉深系數比無凸緣圓筒形的小。而且當坯料直徑D一定時,凸緣相對直徑dt/d越大,極限拉深系數越小,這是因為
39、在坯料直徑D和圓筒形直徑d一定的情況下,帶凸緣圓筒形件的凸緣相對直徑dt/d大,意味著只要將坯料直徑稍加收縮即可達到零件凸緣外徑,筒壁傳力區的拉應力遠沒有達到許可值,因而可以減小其拉深系數。但這并不表明帶凸緣圓筒形件的變形程度大。由上述分析可知,在影響mt的因素中,因R/d影響較小,因此當mt一定時,則dt/d與H/d的關系也就基本確定了。這樣,就可用拉深件的相對高度來表示帶凸緣圓筒形件的變形程度。首次拉深可能達到的相對高度見表5-13。當帶凸緣圓筒形件的總拉深系數mt=d/D大于表5-12的極限拉深系數,且零件的相對高度H/d小于表5-13的極限值時,則可以一次拉深成形,否則需要兩次或多次拉
40、深。帶凸緣圓筒形件以后各次拉深系數為: mi=di/ di-1 (i=2、3、n) (5-8)其值與凸緣寬度及外形尺寸無關,可取與無凸緣圓筒形件的相應拉深系數相等或略小的數值,見表(4) 帶凸緣圓筒形件的各次拉深高度根據帶凸緣圓筒形件坯料直徑計算公式(見表5-6),可推導出各次拉深高度的計算公式如下:(i=1、2、3、n) (5-9)式中 H1、H2、Hn各次拉深工序件的高度; d1、d2、dn各次拉深工序件的直徑; D坯料直徑; r1、r2、rn各次拉深工序件的底部圓角半徑; R1、R2、Rn各次拉深工序件的凸緣圓角半徑。(5) 帶凸緣圓筒形件的拉深工序尺寸計算程序帶凸緣圓筒形件拉深與無凸緣
41、圓筒形件拉深的最大區別在于首次拉深,現結合實例說明其工序尺寸計算程序。例5-3 試對圖5-20所示帶凸緣圓筒形件的拉深工序進行計算。零件材料為08鋼,厚度t=1mm。圖5-20 帶凸緣圓筒形件解:板料厚度t=1mm,故按中線尺寸計算。(1) 計算坯料直徑D 根據零件尺寸查表5-5得切邊余量R=2.2mm,故實際凸緣直徑dt =(55.4+22.2)=59.8mm。由表5-6查得帶凸緣圓筒形件的坯料直徑計算公式為D =依圖5-20,d1=16.1mm,R=r=2.5mm,d2=21.1mm,h=27mm,d3=26.1mm,d4=59.8mm,代入上式得D=78(mm)(其中3200/4為該拉深
42、件除去凸緣平面部分的表面積)(2) 判斷可否一次拉深成形 根據t/D =1/78 = 1.28 %dt/d = 59.8/21.1 = 2.83H/d = 32/21.1 =1. 52 mt=d/D=21.1/78=0.27查表5-12、表5-13,m1=0.35,H1/d1=0.21,說明該零件不能一次拉深成形,需要多次拉深。(3) 確定首次拉深工序件尺寸 初定dt/d1=1.3,查表5-12得m1=0.51,取m1= 0.52,則d1= m1 D = 0.5278 = 40.5(mm)取r1=R1= 5.5 mm 為了使以后各次拉深時凸緣不再變形,取首次拉入凹模的材料面積比最后一次拉入凹模
43、的材料面積(即零件中除去凸緣平面以外的表面積3200/4)增加5%,故坯料直徑修正為D=79(mm)按式(5-9),可得首次拉深高度為 H1 =21.2(mm)驗算所取m1是否合理:根據t/D =1.28 %,dt/d1 = 59.8/40.5=1.48,查表5-13可知H1/d1= 0.58。因H1/d1 =21.2/40.5= 0.52H1/d1= 0.58,故所取m1是合理的。(4) 計算以后各次拉深的工序件尺寸 查表5-14得,m2= 0.75,m3= 0.78,m 4= 0.80,則d2= m2 d1= 0.7540.5 = 30.4(mm)d3= m3 d2 = 0.7830.4
44、= 23.7(mm)d4= m4 d3 = 0.8023.7 = 19.0(mm)因d4= 19.021.1,故共需4次拉深。調整以后各次拉深系數,取m2 = 0.77,m3 = 0.80,m 4 = 0.844。故以后各次拉深工序件的直徑為 d2= m2 d1= 0.7740.5 = 31.2(mm)d3= m3 d2 = 0.8031.2 = 25.0(mm)d4= m4 d3 = 0.84425.0= 21.1(mm)以后各次拉深工序件的圓角半徑取 r2=R2=4.5mm,r3=R3=3.5mm,r4=R4=2.5mm設第二次拉深時多拉入3%的材料(其余2%的材料返回到凸緣上),第三次拉
45、深時多拉入1.5%的材料(其余1.5%的材料返回到凸緣上),則第二次和第三次拉深的假想坯料直徑分別為=78.7(mm)=78.4(mm) 以后各次拉深工序件的高度為H2 =24.8(mm)H3 =28.7(mm) 圖5-21 帶凸緣圓筒形件的各次拉深工序尺寸最后一次拉深后達到零件的高度H4=32mm,上工序多拉入的1.5%的材料全部返回到凸緣,拉深工序至此結束。將上述按中線尺寸計算的工序件尺寸換算成與零件圖相同的標注形式后,所得各工序件的尺寸如圖5-21所示。5.5 圓筒形件的拉深力、壓料力與壓料裝置5.5.1 拉深力的確定圖5-22所示為試驗測得一般情況下的拉深力隨凸模行程變化的曲線。圖5-
46、22 拉深力變化曲線由于影響拉深力的因素比較復雜,按實際受力和變形情況來準確計算拉深力是比較困難的,所以,實際生產中通常是以危險斷面的拉應力不超過其材料抗拉強度為依據,采用經驗公式進行計算。對于圓筒形件:首次拉深 F=K1d1tb (5-10) 以后各次拉深 F =K2di tb (i=2、3、n) (5-11)式中 F拉深力d1、d2、dn各次拉深工序件直徑(mm);t板料厚度(mm);b拉深件材料的抗拉強度(MPa);K1、K2修正系數,與拉深系數有關,見表5-15。5.5.2 壓料力的確定 壓料力的作用是防止拉深過程中坯料的起皺。壓料力的大小應適當,壓料力過小時,防皺效果不好;壓料力過大
47、時,則會增大傳力區危險斷面上的拉應力,從而引起嚴重變薄甚至拉裂。因此,應在保證坯料變形區不起皺的前提下,盡量選用較小的壓料力。應該指出,壓料力的大小應允許在一定范圍內調節。一般來說,隨著拉深系數的減小,壓料力許可調節范圍減小,這對拉深工作是不利的,因為這時當壓料力稍大些時就會產生破裂,壓料力稍小些時會產生起皺,也即拉深的工藝穩定性不好。相反,拉深系數較大時,壓料力可調節范圍增大,工藝穩定性較好。在模具設計時,壓料力可按下列經驗公式計算:任何形狀的拉深件 FY=Ap (5-12)圓筒形件首次拉深 FY=p/4 (5-13)圓筒形件以后各次拉深 FY=p/4 (i=2、3、) (5-14)式中 F
48、Y壓料力(N);A壓料圈下坯料的投影面積(mm2); p單位面積壓料力(MPa),可查表5-16; D坯料直徑(mm);d1、d2、dn各次拉深工序件的直徑(mm);rA1、rA2、rAn各次拉深凹模的圓角半徑(mm)。5.5.3 壓料裝置目前生產中常用的壓料裝置有彈性壓料裝置和剛性壓料裝置。1彈性壓料裝置 在單動壓力機上進行拉深加工時,一般都是采用彈性壓料裝置來產生壓料力。根據產生壓料力的彈性元件不同,彈性壓料裝置可分為彈簧式、橡膠式和氣墊式三種,如圖5-23所示。圖5-23 彈性壓料裝置1-凹模 2-凸模 3-壓料圈 4-彈性元件(彈頂器或氣墊)上述三種壓料裝置的壓料力變化曲線如圖5-24
49、所示。由圖可以看出,彈簧和橡膠壓料裝置的壓料力是隨著工作行程(拉深深度)的增加而增大的,尤其是橡膠式壓料裝置更突出。這樣的壓料力變化特性會使拉深過程中的拉深力不斷增大,從而增大拉裂的危險性。因此,彈簧和橡膠壓料裝置通常只用于淺拉深。但是,這兩種壓料裝置結構簡單,在中小型壓力機上使用較為方便。只要正確地選用彈簧的規格和橡膠的牌號及尺寸,并采取適當的限位措施,就能減少它的不利方面。彈簧應選總壓縮量大、壓力隨壓縮量增加而緩慢增大的規格。橡膠應選用軟橡膠,并保證相對壓縮量不過大,建議橡膠總厚度不小于拉深工作行程的5倍。氣墊式壓料裝置壓料效果好,壓料力基本上不隨工作行程而變化(壓料力的變化可控制在10%
50、15%內),但氣墊裝置結構復雜。圖5-24 各種彈性壓料裝置的壓料力曲線壓料圈是壓料裝置的關鍵零件,常見的結構形式有平面形、錐形和弧形,如圖5-25所示。一般的拉深模采用平面形壓料圈(圖a);當坯料相對厚度較小,拉深件凸緣小且圓角半徑較大時,則采用帶弧形的壓料圈(圖c);錐形壓料圈(圖b)能降低極限拉深系數,其錐角與錐形凹模的錐角相對應,一般取=3040,主要用于拉深系數較小的拉深件。圖5-25 壓料圈的結構形式1-凸模 2-頂板 3-凹模 4-壓料圈為了保持整個拉深過程中壓料力均衡和防止將坯料壓得過緊,特別是拉深板料較薄且凸緣較寬的拉深件時,可采用帶限位裝置的壓料圈,如圖5-26所示。限位柱
51、可使壓料圈和凹模之間始終保持一定的距離s。對于帶凸緣零件的拉深,s=t+(0.050.1)mm;鋁合金零件的拉深,s=1.1t;鋼板零件的拉深,s=1.2t(t為板料厚度)。2剛性壓料裝置剛性壓料裝置一般設置在雙動壓力機上用的拉深模中。圖5-27為雙動壓力機用拉深模,件4即為剛性壓料圈(又兼作落料凸模),壓料圈固定在外滑塊之上。在每次沖壓行程開始時,外滑塊帶動壓料圈下降壓在坯料的凸緣上,并在此停止不動,隨后內滑塊帶動凸模下降,并進行拉深變形。剛性壓料裝置的壓料作用是通過調整壓料圈與凹模平面之間的間隙c獲得的,而該間隙則靠調節壓力機外滑塊得到。考慮到拉深過程中坯料凸緣區有增厚現象,所以這一間隙應略大于板料厚度。剛性壓料圈的結構形式與彈性壓料圈基本相同。剛性壓料裝置的特點是壓料力不隨拉深的工作行程而變化,壓料效果較好,模具結構簡單。圖5-26 有限位裝置的壓料圈圖5-27 雙動壓力機用拉深模的剛性壓料1-凸模固定桿 2-外滑塊 3-拉深凸模 4-壓料圈兼落料凸模 5-落料凹模 6-拉深凹模拉深時的起皺和防止起皺的問題比較復雜,防皺的壓料與防破裂又有矛盾,目前常用的壓料裝置產生的壓料力還不能符合理想的壓料力變化曲線。因此,如何探索較理想的壓料裝置是拉深工作的一個重要課題。5.5.4 拉深壓力機標稱壓
溫馨提示
- 1. 本站所有資源如無特殊說明,都需要本地電腦安裝OFFICE2007和PDF閱讀器。圖紙軟件為CAD,CAXA,PROE,UG,SolidWorks等.壓縮文件請下載最新的WinRAR軟件解壓。
- 2. 本站的文檔不包含任何第三方提供的附件圖紙等,如果需要附件,請聯系上傳者。文件的所有權益歸上傳用戶所有。
- 3. 本站RAR壓縮包中若帶圖紙,網頁內容里面會有圖紙預覽,若沒有圖紙預覽就沒有圖紙。
- 4. 未經權益所有人同意不得將文件中的內容挪作商業或盈利用途。
- 5. 人人文庫網僅提供信息存儲空間,僅對用戶上傳內容的表現方式做保護處理,對用戶上傳分享的文檔內容本身不做任何修改或編輯,并不能對任何下載內容負責。
- 6. 下載文件中如有侵權或不適當內容,請與我們聯系,我們立即糾正。
- 7. 本站不保證下載資源的準確性、安全性和完整性, 同時也不承擔用戶因使用這些下載資源對自己和他人造成任何形式的傷害或損失。
最新文檔
- 2025版農村房產交易合同
- 2025農村集體土地使用權流轉合同(受讓方)
- 2025合作伙伴產品合同樣本
- 2025健身房加盟合同范本
- 2025年安全防護欄安裝合同
- 2025華能物流季度結服務合同
- 2025合同終止勞動合同的法律責任
- 2025年土地租賃意向合同
- 2025【工程勞務合同】工程勞務合同
- 《原子與分子揭示了》課件
- 2025年裝維智企工程師(三級)復習模擬100題及答案
- 國家管網集團西南管道昆明輸油氣分公司突發環境事件綜合應急預案
- 2024國家能源集團新疆哈密能源化工有限公司社會招聘110人筆試參考題庫附帶答案詳解
- 糖尿病飲食與護理
- 2025年天津市河東區中考一模歷史試題(原卷版+解析版)
- 停送電培訓課件
- 醫院培訓課件:《核心制度-護理值班和交接班制度》
- 解題秘籍05 圓的綜合問題(9種題型匯-總+專題訓練)(解析版)-2025年中考數學重難點突破
- 《基于STM32的智能水質檢測系統的設計》9400字(論文)
- 無線網絡施工方案
- 電商平臺居間合同
評論
0/150
提交評論